Molybdenum (Mo). These steels will be discussed at more length in
Chapters III and IV.
PROPERTIES OF STEEL
Steels are known by certain tests. Early tests were more or less crude,
and depended upon the ability of the workman to judge the "grain"
exhibited by a freshly broken piece of steel. The cold-bend test was
also very useful--a small bar was bent flat upon itself, and the stretched
fibers examined for any sign of break. Harder stiff steels were
supported at the ends and the amount of central load they would
support before fracture, or the amount of permanent set they would
acquire at a given load noted. Files were also used to test the hardness
of very hard steel.
These tests are still used to a considerable extent, especially in works
where the progress of an operation can be kept under close watch in
this way, the product being periodically examined by more precise
methods. The chief furnace-man, or "melter," in a steel plant, judges
the course of the refining process by casting small test ingots from time
to time, breaking them and examining the fracture. Cutlery
manufacturers use the bend test to judge the temper of blades. File
testing of case-hardened parts is very common.
However there is need of standardized methods which depend less
upon the individual skill of the operator, and which will yield results
comparable to others made by different men at different places and on
different steels. Hence has grown up the art of testing materials.
TENSILE PROPERTIES
Strength of a metal is usually expressed in the number of pounds a 1-in.
bar will support just before breaking, a term called the "ultimate
strength." It has been found that the shape of the test bar and its method
of loading has some effect upon the results, so it is now usual to turn a
rod 5-1/2 in. long down to 0.505 in. in diameter for a central length of
2-3/8 in., ending the turn with 1/2-in. fillets. The area of the bar equals
0.2 sq. in., so the load it bears at rupture multiplied by 5 will represent
the "ultimate strength" in pounds per square inch.
Such a test bar is stretched apart in a machine like that shown in Fig. 9.
The upper end of the bar is held in wedged jaws by the top cross-head,
and the lower end grasped by the movable head. The latter is moved up
and down by three long screws, driven at the same speed, which pass
through threads cut in the corners of the cross-head. When the test
piece is fixed in position the motor which drives the machine is given a
few turns, which by proper gearing pulls the cross-head down with a
certain pull. This pull is transmitted to the upper cross-head by the test
bar, and can be weighed on the scale arm, acting through a system of
links and levers.
Thus the load may be increased as rapidly as desirable, always kept
balanced by the weighing mechanism, and the load at fracture may be
read directly from the scale beam.
This same test piece may give other information. If light punch marks
are made, 2 in. apart, before the test is begun, the broken ends may be
clamped together, and the distance between punch marks measured. If
it now measures 3 in. the stretch has been 1 in. in 2, or 50 per cent. This
figure is known as the elongation at fracture, or briefly, the
"elongation," and is generally taken to be a measure of ductility.
When steel shows any elongation, it also contracts in area at the same
time. Often this contraction is sharply localized at the fracture; the
piece is said to "neck." A figure for contraction in area is also of much
interest as an indication of toughness; the diameter at fracture is
measured, a corresponding area taken out from a table of circles,
subtracted from the original area (0.200 sq. in.) and the difference
divided by 0.2 to get the percentage contraction.
[Illustration: FIG. 9.--Olsen testing machine.]
Quite often it is desired to discover the elastic limit of the steel, in fact
this is of more use to the designer than the ultimate strength. The elastic
limit is usually very close to the load where the metal takes on a
permanent set. That is to say, if a delicate caliper ("extensometer," so
called) be fixed to the side of the test specimen, it would show the
piece to be somewhat longer under load than when free. Furthermore, if
the load had not yet reached the yield point, and were released at any
time, the piece would return to its original length. However, if the load
had been excessive, and then relieved, the extensometer would no
longer read exactly 2.0
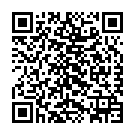
Continue reading on your phone by scaning this QR Code
Tip: The current page has been bookmarked automatically. If you wish to continue reading later, just open the
Dertz Homepage, and click on the 'continue reading' link at the bottom of the page.