in., but something more.
Soft steels "give" very quickly at the yield point. In fact, if the testing
machine is running slowly, it takes some time for the lower head to
catch up with the stretching steel. Consequently at the yield point, the
top head is suddenly but only temporarily relieved of load, and the
scale beam drops. In commercial practice, the yield point is therefore
determined by the "drop of the beam." For more precise work the
calipers are read at intervals of 500 or 1,000 lb. load, and a curve
plotted from these results, a curve which runs straight up to the elastic
limit, but there bends off.
A tensile test therefore gives four properties of great usefulness: The
yield point, the ultimate strength, the elongation and the contraction.
Compression tests are seldom made, since the action of metal in
compression and in tension is closely allied, and the designer is usually
satisfied with the latter.
IMPACT TESTS
Impact tests are of considerable importance as an indication of how a
metal will perform under shock. Some engineers think that the tensile
test, which is one made under slow loading, should therefore be
supplemented by another showing what will happen if the load is
applied almost instantaneously. This test, however, has not been
standardized, and depends to a considerable extent upon the type of
machine, but more especially the size of the specimen and the way it is
"nicked." The machine is generally a swinging heavy pendulum. It falls
a certain height, strikes the sample at the lowest point, and swings on
past. The difference between the downward and upward swing is a
measure of the energy it took to break the test piece.
FATIGUE TESTS
It has been known for fifty years that a beam or rod would fail at a
relatively low stress if only repeated often enough. It has been found,
however, that each material possesses a limiting stress, or endurance
limit, within which it is safe, no matter how often the loading occurs.
That limiting stress for all steels so far investigated causes fracture
below 10 million reversals. In other words, a steel which will not break
before 10,000,000 reversals can confidently be expected to endure
100,000,000, and doubtless into the billions.
About the only way to test one piece such a large number of times is to
fashion it into a beam, load it, and then turn the beam in its supports.
Thus the stress in the outer fibers of the bar varies from a maximum
stretch through zero to a maximum compression, and back again. A
simple machine of this sort is shown in Fig. 10, where B and E are
bearings, A the test piece, turned slightly down in the center, C and D
ball bearings supporting a load W. K is a pulley for driving the machine
and N is a counter.
[Illustration: FIG. 10.--Sketch of rotating beam machine for measuring
endurance of metal.]
HARDNESS TESTING
The word "hardness" is used to express various properties of metals,
and is measured in as many different ways.
"Scratch hardness" is used by the geologist, who has constructed
"Moh's scale" as follows:
Talc has a hardness of 1 Rock Salt has a hardness of 2 Calcite has a
hardness of 3 Fluorite has a hardness of 4 Apatite has a hardness of 5
Feldspar has a hardness of 6 Quartz has a hardness of 7 Topaz has a
hardness of 8 Corundum has a hardness of 9 Diamond has a hardness of
10
A mineral will scratch all those above it in the series, and will be
scratched by those below. A weighted diamond cone drawn slowly over
a surface will leave a path the width of which (measured by a
microscope) varies inversely as the scratch hardness.
"Cutting hardness" is measured by a standardized drilling machine, and
has a limited application in machine-shop practice.
"Rebounding hardness" is commonly measured by the Shore
scleroscope, illustrated in Fig. 11. A small steel hammer, 1/4 in. in
diameter, 3/4 in. in length, and weighing about 1/12 oz. is dropped a
distance of 10 in. upon the test piece. The height of rebound in arbitrary
units represents the hardness numeral.
[Illustration: FIG. 11.--Shore scleroscope.]
Should the hammer have a hard flat surface and drop on steel so hard
that no impression were made, it would rebound about 90 per cent of
the fall. The point, however, consists of a slightly spherical, blunt
diamond nose 0.02 in. in diameter, which will indent the steel to a
certain extent. The work required to make the indentation is taken from
the energy of the falling body; the rebound will absorb the balance, and
the hammer will now rise from the same steel a distance equal to about
75 per cent of the fall.
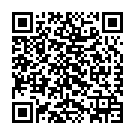
Continue reading on your phone by scaning this QR Code
Tip: The current page has been bookmarked automatically. If you wish to continue reading later, just open the
Dertz Homepage, and click on the 'continue reading' link at the bottom of the page.