many specifications do not set any limit on
sulphur, resting on the idea that if sulphur is low enough not to cause
trouble to the manufacturer during rolling, it will not cause the user any
trouble.
Tool steel and other fine steels should be very low in sulphur,
preferably not higher than 0.03 per cent. Higher sulphur steels (0.06 per
cent, and even up to 0.10 per cent) have given very good service for
machine parts, but in general a high sulphur steel is a suspicious steel.
Screw stock is purposely made with up to 0.12 per cent sulphur and a
like amount of phosphorus so it will cut freely.
Manganese counteracts the detrimental effect of sulphur when present
in the steel to an amount at least five times the sulphur content.
PHOSPHORUS is an element (symbol P) which enters the metal from
the ore. It remains in the steel when made by the so-called acid process,
but it can be easily eliminated down to 0.06 per cent in the basic
process. In fact the discovery of the basic process was necessary before
the huge iron deposits of Belgium and the Franco-German border could
be used. These ores contain several per cent phosphorus, and made a
very brittle steel ("cold short") until basic furnaces were used. Basic
furnaces allow the formation of a slag high in lime, which takes
practically all the phosphorus out of the metal. Not only is the resulting
metal usable, but the slag makes a very excellent fertilizer, and is in
good demand.
SILICON is a very widespread element (symbol Si), being an essential
constituent of nearly all the rocks of the earth. It is similar to carbon in
many of its chemical properties; for instance it burns very readily in
oxygen, and consequently native silicon is unknown--it is always found
in combination with one or more other elements. When it bums, each
atom of silicon unites with two atoms of oxygen to form a compound
known to chemists as silica (SiO2), and to the small boy as "sand" and
"agate."
Iron ore (an oxide of iron) contains more or less sand and dirt mixed in
it when it is mined, and not only the iron oxide but also some of the
silicon oxide is robbed of its oxygen by the smelting process. Pig
iron--the product of the blast furnace--therefore contains from 1 to 3
per cent of silicon, and some silicon remains in the metal after it has
been purified and converted into steel.
However, silicon, as noted above, burns very readily in oxygen, and
this property is of good use in steel making. At the end of the
steel-making process the metal contains more or less oxygen, which
must be removed. This is sometimes done (especially in the so-called
acid process) by adding a small amount of silicon to the hot metal just
before it leaves the furnace, and stirring it in. It thereupon abstracts
oxygen from the metal wherever it finds it, changing to silica (SiO2)
which rises and floats on the surface of the cleaned metal. Most of the
silicon remaining in the metal is an excess over that which is required
to remove the dangerous oxygen, and the final analysis of many steels
show enough silicon (from 0.20 to 0.40) to make sure that this step in
the manufacture has been properly done.
MANGANESE is a metal much like iron. Its chemical symbol is Mn. It
is somewhat more active than iron in many chemical changes--notably
it has what is apparently a stronger attraction for oxygen and sulphur
than has iron. Therefore the metal is used (especially in the so-called
basic process) to free the molten steel of oxygen, acting in a manner
similar to silicon, as explained above. The compound of manganese
and oxygen is readily eliminated from the metal. Sufficient excess of
elemental manganese should remain so that the purchaser may be sure
that the iron has been properly "deoxidized," and to render harmless the
traces of sulphur present. No damage is done by the presence of a little
manganese in steel, quite the reverse. Consequently it is common to
find steels containing from 0.3 to 1.5 per cent.
ALLOYING ELEMENTS.--Commercial steels of even the simplest
types are therefore primarily alloys of iron and carbon. Impurities and
their "remedies" are always present: sulphur, phosphorus, silicon and
manganese--to say nothing of oxygen, nitrogen and carbon oxide gases,
about which we know very little. It has been found that other metals, if
added to well-made steel, produce definite improvements in certain
directions, and these "alloy steels" have found much use in the last ten
years. Alloy steels, in addition to the above-mentioned elements, may
commonly contain one or more of the following, in varying amounts:
Nickel (Ni), Chromium (Cr), Vanadium (Va), Tungsten (W),
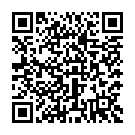
Continue reading on your phone by scaning this QR Code
Tip: The current page has been bookmarked automatically. If you wish to continue reading later, just open the
Dertz Homepage, and click on the 'continue reading' link at the bottom of the page.