to prevent rephosphorizing and to permit of adding carburizing materials. For this purpose carbon is added in the form of powdered coke, ground electrodes or other forms of pure carbon.
The deoxidizing slag is now formed by additions of lime, coke and fluorspar (and for some analyses ferrosilicon). The slag changes from black to white as the metallic oxides are reduced by these deoxidizing additions and the reduced metals return to the bath. A good finishing slag is creamy white, porous and viscous. After the slag becomes white, some time is necessary for the absorption of the sulphur in the bath by the slag.
The white slag disintegrates to a powder when exposed to the atmosphere and has a pronounced odor of acetylene when wet.
Further additions of recarburizing material are added as needed to meet the analysis. The further reactions are shown by the following:
3:40 P.M.--Recarburizing material added: 130 lb. ground electrodes. 25 lb. ferromanganese. Analysis: Carbon Silicon Sulphur Phosphorus Manganese 0.76 0.011 0.030 0.008 0.26
To form white slag there was added:
225 lb. lime. 75 lb. powdered coke. 55 lb. fluorspar. 4:50 P.M.-- Analysis: Carbon Silicon Sulphur Phosphorus Manganese 0.75 0.014 0.012 0.008 0.28 Note reduction of the sulphur content.
During the white-slag period the following alloying additions were made:
500 lb. pig iron. 80 lb. ferrosilicon. 9 lb. ferromanganese. 146 lb. 6 per cent carbon ferrochrome.
The furnace was rotated forward to an inclined position and the charge poured into the ladle, from which in turn it was poured into molds.
5:40 P.M.--Heat poured. Analysis: Carbon Silicon Sulphur Phosphorus Manganese Chromium 0.97 0.25 0.014 0.013 0.33 0.70
Ingot weight poured 94.0 per cent Scull 2.7 per cent Loss 3.3 per cent
Total current consumption for the heat, 4,700 kW.-hr. or 710 kw.-hr. per ton.
Electric steel, in fact, all fine steel, should be cast in big-end-up molds with refractory hot tops to prevent any possibility of pipage in the body of the ingot. In the further processing of the ingot, whether in the rolling mill or forge, special precautions should be taken in the heating, in the reduction of the metal and in the cooling.
No attempt is made to compare the relative merits of open hearth and electric steel; results in service, day in and day out, have, however, thoroughly established the desirability of electric steel. Ten years of experience indicate that electric steel is equal to crucible steel and superior to open hearth.
The rare purity of the heat derived from the electric are, combined with definite control of the slag in a neutral atmosphere, explains in part the superiority of electric steel. Commenting on this recently Dr. H. M. Howe stated that "in the open hearth process you have such atmosphere and slag conditions as you can get, and in the electric you have such atmosphere and slag conditions as you desire."
Another type of electric furnace is shown in Figs. 7 and 8. This is the Ludlum furnace, the illustrations showing a 10-ton size. Figure 7 shows it in normal, or melting position, while in Fig. 8 it is tilted for pouring. In melting, the electrodes first rest on the charge of material in the furnace. After the current is turned on they eat their way through, nearly to the bottom. By this time there is a pool of molten metal beneath the electrode and the charge is melted from the bottom up so that the roof is not exposed to the high temperature radiating from the open arc. The electrodes in this furnace are of graphite, 9 in. in diameter and the current consumed is about 500 kw.-hr. per ton.
[Illustration: FIG. 7.--Ludlum electric furnace.]
[Illustration: FIG. S.--The furnace tilted for pouring.]
One of the things which sometimes confuse regarding the contents of steel is the fact that the percentage of carbon and the other alloys are usually designated in different ways. Carbon is usually designated by "points" and the other alloys by percentages. The point is one ten-thousandth while 1 per cent is one one-hundredth of the whole. In other words, "one hundred point carbon" is steel containing 1 per cent carbon. Twenty point carbon, such as is used for carbonizing purposes is 0.20 per cent. Tool steel varies from one hundred to one hundred and fifty points carbon, or from 1.00 to 1.50 per cent.
Nickel, chromium, etc., are always given in per cent, as a 3.5 per cent nickel, which means exactly what it says--3-1/2 parts in 100. Bearing this difference in mind all confusion will be avoided.
CLASSIFICATIONS OF STEEL
Among makers and sellers, carbon tool-steels are classed by "grade" and "temper." The word grade is qualified by many adjectives of more or less cryptic meaning, but in general they aim to denote the process and care with which the steel is made.
Temper of a steel refers to the carbon content. This should preferably be noted by "points,"
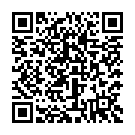
Continue reading on your phone by scaning this QR Code
Tip: The current page has been bookmarked automatically. If you wish to continue reading later, just open the
Dertz Homepage, and click on the 'continue reading' link at the bottom of the page.