aids materially in the refining operations.
In the bessemer process air is forced through the metal. In the
open-hearth furnace the metal is protected from the flaming gases by a
slag covering. Therefore it is reasonable to suppose that the final
product will not contain so much gas.
[Illustration: FIG. 2.--Action of Bessemer converter.]
[Illustration: FIG. 3.--Regenerative open hearth furnace.]
A diagram of a modern regenerative furnace is shown in Fig. 3. Air and
gas enter the hearth through chambers loosely packed with hot fire
brick, burn, and exit to the chimney through another pair of chambers,
giving to them some of the heat which would otherwise waste. The
direction is reversed about every twenty minutes by changing the
position of the dampers.
CRUCIBLE STEEL
Crucible steel is still made by melting material in a clay or graphite
crucible. Each crucible contains about 40 lb. of best puddled iron, 40 lb.
of clean "mill scrap"--ends trimmed from tool steel bars--and sufficient
rich alloys and charcoal to make the mixture conform to the desired
chemical analysis. The crucible is covered, lowered into a melting hole
(Fig. 4) and entirely surrounded by burning coke. In about four hours
the metal is converted into a quiet white hot liquid. Several crucibles
are then pulled out of the hole, and their contents carefully poured into
a metal mold, forming an ingot.
[Illustration: FIG. 4.--Typical crucible furnace.]
If modern high-speed steel is being made, the ingots are taken out of
the molds while still red hot and placed in a furnace which keeps them
at this temperature for some hours, an operation known as annealing.
After slow cooling any surface defects are ground out. Ingots are then
reheated to forging temperature, hammered down into "billets" of about
one-quarter size, and 10 to 20 per cent of the length cut from the top.
After reheating the billets are hammered or rolled into bars of desired
size. Finished bars are packed with a little charcoal into large pipes, the
ends sealed, and annealed for two or three days. After careful
inspection and testing the steel is ready for market.
THE ELECTRIC PROCESS
The fourth method of manufacturing steel is by the electric furnace.
These furnaces are of various sizes and designs; their size may be
sufficient for only 100 lb. of metal--on the other hand electric furnaces
for making armor-plate steel will hold 40 tons of steel. Designs vary
widely according to the electrical principles used. A popular furnace is
the 6-ton Heroult furnace illustrated in Fig. 5.
It is seen to be a squat kettle, made of heavy sheet steel, with a dished
bottom and mounted so it can be tilted forward slightly and completely
drained. This kettle is lined with special fire brick which will withstand
most intense heat and resist the cutting action of hot metal and slag. For
a roof, a low dome of fire brick is provided. The shell and lining is
pierced in front for a pouring spout, and on either side by doors,
through which the raw material is charged.
Two or three carbon "electrodes"--18-in. cylinders of specially
prepared coke or graphite--extend through holes in the roof. Electrical
connections are made to the upper ends, and a very high current sent
through them. This causes tremendous arcs to form between the lower
ends of the electrodes and the metal below, and these electric arcs are
the only source of heat in this style of furnace.
Electric furnaces can be used to do the same work as is done in crucible
furnaces--that is to say, merely melt a charge of carefully selected pure
raw materials. On the other hand it can be used to produce very
high-grade steel from cheap and impure metal, when it acts more like
an open-hearth furnace. It can push the refining even further than the
latter furnace does, for two reasons: first the bath is not swept
continuously by a flaming mass of gases; second, the temperature can
be run up higher, enabling the operator to make up slags which are
difficult to melt but very useful to remove small traces of impurities
from the metal.
Electric furnaces are widely used, not only in the iron industry, but in
brass, copper and aluminum works. It is a useful melter of cold metal
for making castings. It can be used to convert iron into steel or vice
versa. Its most useful sphere, however, is as a refiner of metal, wherein
it takes either cold steel or molten steel from open hearth or bessemer
furnaces, and gives it the finishing touches.
[Illustration: FIG. 5.--"Slagging off" an electric furnace.]
[Illustration: FIG. 6.--Pouring the ingots.]
As an illustration of the furnace reactions that take place the following
schedule is given, showing the various stages in the making of a heat of
electric steel.
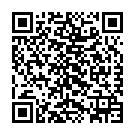
Continue reading on your phone by scaning this QR Code
Tip: The current page has been bookmarked automatically. If you wish to continue reading later, just open the
Dertz Homepage, and click on the 'continue reading' link at the bottom of the page.