is therefore called
graphitic carbon. The resemblance can be seen by noting how cast-iron
borings blacken the hands just as does graphite, while steel turnings do
not have the same effect. The difference is due to the fact that the
carbon in steel is not in a graphitic form as well as because it is present
in smaller quantities.
In making steel in the old way the cast iron was melted and the carbon
and other impurities burned out of it, the melted iron being stirred or
"puddled," meanwhile. The resulting puddled iron, also known as
wrought iron, is very low in carbon; it is tough, and on being broken
appears to be made up of a bundle of long fibers. Then the iron was
heated to redness for several days in material containing carbon
(charcoal) until it absorbed the desired amount, which made it steel,
just as case-hardening iron or steel adds carbon to the outer surface of
the metal. The carbon absorbed by the iron does not take on a graphitic
form, however, as in the case of cast iron, but enters into a chemical
compound with the iron, a hard brittle substance called "cementite" by
metallurgists. In fact, the difference between the hard, brittle cementite
and the soft, greasy graphite, accounts for many of the differences
between steel and gray cast iron. Wrought iron, which has very little
carbon of any sort in it, is fairly soft and tough. The properties of
wrought iron are the properties of pure iron. As more and more carbon
is introduced into the iron, it combines with the iron and distributes
itself throughout the metal in extremely small crystals of cementite, and
this brittle, hard substance lends more and more hardness and strength
to the steel, at the expense of the original toughness of the iron. As
more and more carbon is contained in the alloy--for steel is a true
alloy--it begins to appear as graphite, and its properties counteract the
remaining brittle cementite. Eventually, in gray cast iron, we have
properties which would be expected of wrought iron, whose tough
metallic texture was shot through with flakes of slippery, weak
graphite.
But to return to the methods of making steel tools in use 100 years ago.
The iron bars, after heating in charcoal, were broken and the carbon
content judged by the fracture. Those which had been in the hottest part
of the furnace would have the deepest "case" and highest carbon. So
when the steel was graded, and separated into different piles, a few bars
of like kind were broken into short lengths, melted in fire-clay crucibles
at an intense white heat, cast carefully into iron molds, and the resulting
ingot forged into bars under a crude trip hammer. This melting practice
is still in use for crucible steel, and will be described further on page 4.
THE WORKING OF STEEL
ANNEALING, HEAT TREATING AND HARDENING
OF
CARBON AND ALLOY STEEL
CHAPTER I
STEEL MAKING
There are four processes now used for the manufacture of steel. These
are: The Bessemer, Open Hearth, Crucible and Electric Furnace
Methods.
BESSEMER PROCESS
The bessemer process consists of charging molten pig iron into a huge,
brick-lined pot called the bessemer converter, and then in blowing a
current of air through holes in the bottom of the vessel into the liquid
metal.
The air blast burns the white hot metal, and the temperature increases.
The action is exactly similar to what happens in a fire box under forced
draft. And in both cases some parts of the material burn easier and
more quickly than others. Thus it is that some of the impurities in the
pig iron--including the carbon--burn first, and if the blast is shut off
when they are gone but little of the iron is destroyed. Unfortunately
sulphur, one of the most dangerous impurities, is not expelled in the
process.
A bessemer converter is shown in Fig. 1, while Fig. 2 shows the details
of its construction. This shows how the air blast is forced in from one
side, through the trunnion, and up through the metal. Where the steel is
finished the converter is tilted, or swung on its trunnions, the blast
turned off, and the steel poured out of the top.
OPEN HEARTH PROCESS
The open hearth furnace consists of a big brick room with a low arched
roof. It is charged with pig iron and scrap through doors in the side
walls.
[Illustration: FIG. 1.--A typical Bessemer converter.]
Through openings at one end of the furnace come hot air and gas,
which burn in the furnace, producing sufficient heat to melt the charge
and refine it of its impurities. Lime and other nonmetallic substances
are put in the furnace. These melt, forming a "slag" which floats on the
metal and
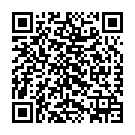
Continue reading on your phone by scaning this QR Code
Tip: The current page has been bookmarked automatically. If you wish to continue reading later, just open the
Dertz Homepage, and click on the 'continue reading' link at the bottom of the page.