which was to cut the rolls into definite
lengths of about ten yards; these were then rerolled very loosely and
immersed in the hot tar until sufficiently saturated. The paper was then
passed through the roller, much pressure exerted, and then loosely
rolled up again. Being tarred once, it was then laid into a second pan
with hot tar, reeled out after a time, strewn with sand, and rolled up
again. Another method was to cut clothes lines into lengths of about
fifteen yards, and at a distance of two inches have knots tied in them.
The paper was cut in lengths of ten or fifteen yards, three pieces of the
knotted clothes line were then rolled between the loose coils of paper,
which was then submerged in the tar, which on account of the knots
could penetrate the paper. The paper was next sanded by permitting its
lower surface to pass over dry sand in a box standing on the floor. A
workman rolled off the paper, and with his hand he strews sand on the
upper surface. The rolling taking place on the edge of a table, by means
of a crank, the excess of sand dropped off.
It is said by this method two workmen, one of which tends to the
rolling and sanding, the other turning the crank, could turn out eighty
rolls per day. This method is still in use. It is useless to describe the
many antiquated methods in vogue in smaller factories, and it can
truthfully be said that nearly all of them are out of date. It appears to be
the fact of almost all inventions that when reduced to practical use, the
arrangements, apparatus, and working methods employed are generally
of the most complicated nature, and time and experience only will
simplify them. This has been also the case with the methods in the
roofing paper industry, which are at present gradually being reduced to
a practical basis. The method gradually adopted has been described in
the preceding. The pan is of a certain length, whereby it becomes
possible to saturate the paper by slowly drawing it through the heated
tar. This is the chief feature. The work is much simplified thereby and
the workmen need not dip their hands into the tar or soil them with it.
The work of impregnating has become much cleaner and easier, while
at the same time the tar can be heated to a much higher temperature.
The pan is generally filled with distilled coal tar, and the heating is
regulated in such a manner that the temperature of the impregnating
mass is raised far beyond 212° Fahrenheit. This accelerates the
penetration, which takes place more quickly as the degree of heat is
raised, which may be almost up to the boiling point of the tar, as at this
degree the paper is not destroyed by the heat. In order to prevent the
evaporation of the volatile ingredients of the tar, the pan is covered
with a sheet iron cover, with a slot at the place where the paper enters
into the impregnating mass and another at the place where it issues.
The tar is always kept at the same level, by occasional additions.
The roll of paper is mounted upon a shaft at the back end of the pan,
and by suitable arrangement of guide rollers it unwinds slowly, passes
into the tar in which it is kept submerged. The guide rollers can be
raised so that when a new roller is set up they can be raised out of the
tar. The end of the paper is then slipped underneath them above the
surface of the tar, when having passed through the squeezing rollers, it
is fastened to the beaming roller, and the guide rollers are submerged
again. A workman slowly turns the crank of the beaming roller.
This motion draws the paper slowly through the fluid, the roll at the
back end unwinding. The speed with which the squeezing rollers are
turned is regulated in such a manner that the paper remains sufficiently
long underneath the fluid to be thoroughly impregnated with it. The
workmen quickly learn by experience how fast to turn the crank. The
hotter the tar, the more rapid the saturation; the high degree of heat
expels the air and evaporates the hygroscopic fluid in the pores of the
paper. The strong heating of the tar causes another advantage connected
with this method. The surface of the paper as it issues from the
squeezing rollers is still very hot, and a part of the volatile oils
evaporate very quickly at this high temperature. The surface is thereby
at once dried to a certain degree and at the same time receives a
handsome luster, as if it had been coated with a
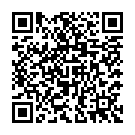
Continue reading on your phone by scaning this QR Code
Tip: The current page has been bookmarked automatically. If you wish to continue reading later, just open the
Dertz Homepage, and click on the 'continue reading' link at the bottom of the page.