Fahrenheit and weighed. To the filtrate is then added a solution of
oxalate of ammonia until a white precipitate of oxalate of lime is
formed. This precipitate is separated by filtering, washed, dried and
when separated from the filter, is collected upon dark satinized paper;
the filter itself is burned and the ash added to the oxalate of lime. This
oxalate of lime is then heated to a dark red heat in a platinum crucible
with lid until the oxalate of lime is converted into carbonate of lime. By
the addition of a few drops of carbonate of ammonia solution and
another slight heating of the crucible, also the caustic lime produced in
the filter ash by heating, is reconverted into carbonate of lime, and after
cooling in the exsiccator, the whole contents of the crucible is weighed
as carbonate of lime, after deducting the known quantity of filter ash.
Any magnesia present in the filtrate of the oxalate of lime is by the
addition of a solution of phosphate of soda separated as phosphate of
ammonia and magnesia, after having stood twenty-four hours. The
precipitate is filtered off, washed with water to which a little chloride of
ammonia is added, dried, and after calcining the fiber and adding the
filter ash, glow heated in the crucible. The glowed substance is weighed
after cooling, and is pyrophosphate of magnesia, from which the
magnesia or carbonate of magnesia is calculated stoichiometrically. All
the ascertained sums must be multiplied by 2, if they are to correspond
to the analyzed and weighed quantity of ash.
The second half of the filtrate is used for determining the small quantity
of sulphate of lime still contained in the hydrochlorate solution. By
adding chloride of barium solution the sulphuric acid is bound to the
barytes and sulphate of baryta separates as white precipitate. This is
separated by filtering, washed, dried and weighed in the customary
manner. From the weight of the sulphate of baryta is then computed the
weight of sulphate of lime, which has passed over into solution. The
ascertained sum is also to be multiplied with 2.
The manufacture of roll tar paper from the roll paper was at first found
to be difficult, as it was impossible to submerge a surface larger than
from ten to fifteen square yards, rolled up, in the tar, because more
would have required too large a pan. Besides this, the paper tears easily,
when it is in the hot tar. All kinds of experiments were tried, in order to
impregnate the surface of the paper without employing too large a pan.
The following method was tried at first: The roll paper was cut into
lengths of ten yards, which were rolled up loosely, so that a certain
space was left between the different coils. These loose rolls, of course,
occupied much space and could be put into the tar only in a standing
position, because in a horizontal one the several coils would have
pressed together again. The loose roll was therefore slipped over a
vertical iron rod fastened into a circular perforated wooden foot. The
upper end of this iron rod ended in a ring, in which the hook of a chain
or rope could be fastened. With the aid of a windlass the roll was raised
or lowered. When placed in the pan with boiling tar, it was left there
until thoroughly saturated. It was then taken out, placed upon a table,
and the excess of tar allowed to drip off into a vessel underneath. After
partially drying, the roll was spread out in open air, occasionally turned,
until sufficiently dried, when it was rolled up again.
In order to neutralize the smeary, sticky condition of the surface and
avoid the disagreeable drying in open air, the experiment of strewing
sand on the sticky places was tried next. The weight of the paper was
largely increased by the sand, and appeared considerably thicker. For
this reason the method of sanding the paper was at once universally
adopted. To dispense with the process of permitting the surplus tar to
drip off, means were devised by which it was taken off by scrapers, or
by pressing through rollers. The scrapers, two sharp edged rods
fastened across the pan, were then so placed that the paper was drawn
through them. The excess of tar adhering to its surface was thereby
scraped off and ran back into the pan.
This work, however, was performed better and to more satisfaction by a
pair of rollers fastened to the pan. These performed a double duty;
thoroughly removed the tar from the surface and by reason of their
pressure they caused a more perfect incorporation of the tar with the
fibers of the paper. Finally, different factories employed different
methods of manufacture, one of
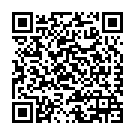
Continue reading on your phone by scaning this QR Code
Tip: The current page has been bookmarked automatically. If you wish to continue reading later, just open the
Dertz Homepage, and click on the 'continue reading' link at the bottom of the page.