kinds, but we remain content with the general remark that they are all
based on the principles of causing revolving knives to operate upon the
rags. The careful cleansing of the cut rags, necessary for the
manufacture of paper, is not required for roofing paper. It is sufficient
to rinse away the sand and other solid extraneous matter. The further
reduction of the cut rags was formerly performed in a stamp mill,
which is no longer employed, the pulp mill or rag engine being
universally used.
The construction of this engine may be described as follows: A box or
trough of wood, iron, or stone is by a partition divided into two parts
which are connected at their ends. At one side upon the bottom of the
box lies an oakwood block, called the back fall. In a hollow of this back
fall is sunk the so-called plate, furnished with a number of sharp steel
cutters or knives, lying alongside of each other. A roller of solid
oakwood, the circumference of which is also furnished with sharp steel
cutters or knives, is fastened upon a shaft and revolves within the
hollow. The journal bearings of the shaft are let into and fastened in
movable wooden carriers. The carriers of the bearings may be raised
and lowered by turning suitable thumbscrews, whereby the distance
between the roller and the back fall is increased or decreased. The
whole is above covered with a dome, the so-called case, to prevent the
throwing out of the mass under the operation of grinding. The roller is
revolved with a velocity of from 100 to 150 revolutions per minute,
whereby the rags are sucked in between the roller and the back fall and
cut and torn between the knives. At the beginning of the operation, the
distance between the roller and the back fall is made as great as
possible, the intention being less to cut the rags than to wash them
thoroughly. The dirty water is then drawn off and replaced by clean,
and the space of the grinding apparatus is lessened gradually, so as to
cut the rags between the knives. The mass is constantly kept in motion
and each piece of rag passes repeatedly between the knives. The case
protects the mass from being thrown out by the centrifugal force. The
work of beating the rags is ended in a few hours, and the ensuing thin
paste is drawn off into the pulp chest, this being a square box lined with
lead.
From the pulp chest it passes to the form of the paper machine. This
form consists of an endless fine web of brass wire, which revolves
around rollers. The upper part of this form rests upon a number of
hollow copper rollers, whereby a level place is formed. The form
revolves uniformly around the two end rollers, and has at the same time
a vibratory motion, by which the pulp running upon the form is spread
out uniformly and conducted along, more flowing on as the latter
progresses. The water escapes rapidly through the close wire web. In
order to limit the form on the sides two endless leather straps revolve
around the rollers on each side, which touch with their lower parts the
form on both sides and confine the fluid within a proper breadth. The
thickness of the pulp is regulated at the head of the form by a brass rule
standing at a certain height; its function is to level the pulp and
distribute it at a certain thickness. The continually moving pulp layer
assumes greater consistency the nearer it approaches to the dandy roll.
This is a cylinder covered with brass wire, and is for the purpose of
compressing the paper, after it has left the form, and free it from a great
part of the water, which escapes into a box. The paper is now freed of a
good deal of the fluid, and assumes a consistency with which it is
enabled to leave the form, which now commences to return underneath
the paper, passing on to an endless felt, which revolves around rollers
and delivers it to two iron rolls. The paper passes through a second pair
of iron rollers, the interiors of which are heated by steam. These rollers
cause the last of the water to be evaporated, so that it can then be rolled
upon reels. A special arrangement shaves the edges to the exact size
required.
The paper is made in different thicknesses and designated by numbers
to the size and weight.
Waste paper, bookbinders' shavings, etc., can be used for making the
paper. As much wool as possible should be employed, because the
wool fiber has a greater resistance than vegetable fiber to the effects of
the temperature. By wool fiber is
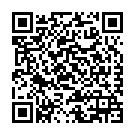
Continue reading on your phone by scaning this QR Code
Tip: The current page has been bookmarked automatically. If you wish to continue reading later, just open the
Dertz Homepage, and click on the 'continue reading' link at the bottom of the page.