especially since the introduction of
the tar distillery, and the manufacture of special roof lacquers, which
have been used for coating in place of the coal tar. As an essential
progress in the tar paper roofing may be mentioned the invention of the
double tar paper roof, and the wood cement roof, which is regarded as
an offshoot.
The tar paper industry has, within the last forty years, assumed great
dimensions, and the preferences for this roofing are gaining ground
daily. In view of the small weight of the covering material, the wood
construction of the roof can be much lighter, and the building is
therefore less strained by the weight of the roof than one with the other
kind, so that the outer walls need not be as heavy. Considering the price,
the paper roof is not only cheaper than other fireproof roofs, but its
light weight makes it possible for the whole building to be constructed
lighter and cheaper. The durability of the tar paper roof is satisfactory,
if carefully made of good material; the double tar paper roof, the gravel
double roof, and the wood cement roof are distinguished by their great
durability.
These roofs may be used for all kinds of buildings, and not only are
factories, storehouses, and country buildings covered with it, but also
many dwellings. The most stylish residences and villas are at present
being inclosed with the more durable kinds; the double roof, the gravel
double roof, and the wood cement roof. For factory buildings, which
are constantly shaken by the vibrations of the machinery, the tar paper
roof is preferable to any other.
In order to ascertain to what degree tar paper roofs would resist fire,
experiments were instituted at the instigation of some of the larger
manufacturers of roofing paper, in the presence of experts, architects,
and others, embracing the most severe tests, and it was fully proved
that the tar paper roof is as fireproof as any other. These experiments
were made in two different ways; first, the readiness of ignition of the
tar paper roof by a spark or flame from the outside was considered, and,
second, it was tested in how far it would resist a fire in the interior of
the building. In the former case, it was ascertained that a bright, intense
fire could be kept burning upon the roof for some time, without igniting
the woodwork of the roof, but heat from above caused some of the
more volatile constituents of the tar to be expelled, whereby small
flames appeared upon the surface within the limits of the fire; the
roofing paper was not completely destroyed. There always remained a
cohesive substance, although it was charred and friable, which by
reason of its bad conductivity of heat protected the roof boarding to
such an extent that it was "browned" only by the developed tar vapors.
A fire was next started within a building covered with a tar paper roof;
the flame touched the roof boarding, which partly commenced to char
and smoulder, but the bright burning of the wood was prevented by the
air-tight condition of the roof; the fire gases could not escape from the
building. The smoke collecting under the roof prevented the entrance of
fresh air, in consequence of which the want of oxygen smothered the
fire. The roofing paper remained unchanged. By making openings in
the sides of the building so that the fire gases could escape, the wood
part of the roof was consumed, but the roofing paper itself was only
charred and did not burn. After removing the fire in contact with the
paper, this ceased burning at once and evinced no disposition whatever
to spread. In large conflagrations, also, the tar paper roofs behaved in
identically a similar manner. Many instances have occurred where the
tar paper roof prevented the fire from spreading inside the building, and
developing with sufficient intensity to work injury.
As it is of interest to the roofer to know the manner of making the
material he uses, we give in the following a short description of the
manufacture of roofing paper. At first, when square sheets were used
exclusively, the raw paper consisted of ordinary dipped or formed
sheets. The materials used in its manufacture were common woolen
rags and other material. In order to prepare the pulp from the rags it is
necessary to cut them so small that the fabric is entirely dissolved and
converted into short fibers. The rags are for this purpose first cut into
pieces, which are again reduced by special machines. The rags are cut
in a rag cutting machine, which was formerly constructed similar to a
feed cutter; later on, more complicated machines of various
constructions were employed. It is not our task to describe the various
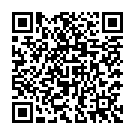
Continue reading on your phone by scaning this QR Code
Tip: The current page has been bookmarked automatically. If you wish to continue reading later, just open the
Dertz Homepage, and click on the 'continue reading' link at the bottom of the page.