required
lining up for nine years. It is, however, a shaft that cannot be inspected
except when in dry dock, and has to be disconnected from the propeller,
and drawn inside for examination at periods suggested by experience.
Serious accidents have occurred through want of attention to the
examination of this shaft; when working in salt water, with liners of
gun metal, galvanic action ensues, and extensive corrosion takes place
in the iron at the ends of the brass liners, more especially if they are
faced up at right angles to the shaft. Some engineers have the
uncovered part of the shaft between the liners, inside the tube, protected
against the sea water by winding over it tarred line. As this may give
out and cause some trouble, by stopping the water space, I have not
adopted it, and shall be pleased to have the experience of any seagoing
engineer on this important matter. A groove round the shaft is formed,
due to this action, and in some cases the shaft has broken inside the
stern tube, breaking not only it, but tearing open the hull, resulting in
the foundering of the vessel. Steel has been used for screw shafts, but
has not been found so suitable, as it corrodes more rapidly in the
presence of salt water and gun metal than iron, and unless protected by
a solid liner for the most part of its length, a mechanical feat which has
not yet been achieved in ordinary construction, as this liner would
require to be 20 ft. long. I find it exceedingly difficult to get a liner of
only 7 ft. long in one piece, and the majority of 6 ft. liners are fitted in
two pieces. The joint of the two liners is rarely watertight, and many
shafts have been destroyed by this method of fitting these liners.
I trust that engine builders will make a step further in the fitting of
these liners on these shafts, as it is against the interest of the shipowner
to keep ships in dry dock from such causes as defective liners, and I
think it will be only a matter of time when the screw shaft will be
completely protected from sea water, at least inside the stern tube; and
when this is done, I would have no hesitation in using steel for screw
shafts. Though an easier forging than a crank shaft, these shafts are
often liable to flaws of a very serious character, owing to the
contraction of the mass of metal forming the coupling; the outside
cooling first tears the center open, and when there is not much metal to
turn off the face of the coupling, it is sometimes undiscovered. Having
observed several of these cavities, some only when the last cut was
being taken off, I have considered it advisable to have holes bored in
the end and center of each coupling, as far through as the thickness of
the flange; when the shafts are of large size, this is sure to find these
flaws out. Another flaw, which has in many cases proved serious when
allowed to extend, is situated immediately abaft the gun metal liner, in
front of the propeller.
This may be induced by corrosion, caused by the presence of sea water,
gun metal, and iron, assisted by the rotation of the shaft. It may also be
caused under heavy strain, owing to the over-finishing of the shaft at
this part under the steam hammer.
The forgemen, in these days of competition and low prices, are
instructed to so finish that there won't be much weight to turn off when
completing the shaft in the lathe. This is effected by the use of
half-round blocks under the hammer, at a lower temperature than the
rest of the forging is done, along with the use of a little water flung on
from time to time; and it is remarkable how near a forging is in truth
when centered in the lathe, and how little there is to come off. The
effect of this manipulation is to form a hard ring of close grain about
one inch thick from the circumference of the shaft inward. The metal in
this ring is much harder than that in the rest of the shaft, and takes all
the strain the inner section gives; consequently, when strain is brought
on, either in heavy weather or should the propeller strike any object at
sea or in the Suez canal, a fracture is caused at the circumference. This,
assisted by slight corrosion, has in my experience led in the course of
four months to a screw shaft being seriously crippled.
I show you a section of a screw shaft found to be flawed, and which I
had broken under the falling weight of
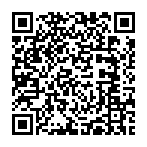
Continue reading on your phone by scaning this QR Code
Tip: The current page has been bookmarked automatically. If you wish to continue reading later, just open the
Dertz Homepage, and click on the 'continue reading' link at the bottom of the page.