only filed to same dimensions, broke at 25 blows. I was well
satisfied with the results, and considered this material, though
possessing a high tensile strength, was in every way suitable for the
construction and endurance required in crank shafts.
Sheet No. 1 shows you some particulars of these tests:
Tensile Elong. Fractured Broke Fall Tons. in 5" Bend. Blows. Blows.
In. A = 30.5 28 p. c. Good 61 78 12
In order to test the comparative value of steel of 24¾ up to 35 tons
tensile strength, I had several specimens taken from shafts tested in the
manner described, which may be called a fatigue test. The results are
shown on the same sheet:
B = 24½ Good 64 72 7 B -- -- -- 48 54 12 C = 27 25.9 p. c. Good 76 81
12 D = 29.6 28.4 p. c. Good 71 78 12 E = 30.5 28.9 p. c. Good 58 77 12
F = 35.5 20 p. c. Good 80 91 12
The latter was very tough to break. Specimen marked A shows one of
these pieces of steel. I show you also fresh broken specimens which
will give you a good idea of the beautiful quality of this material. These
specimens were cut out of shafts made of Steel Co. of Scotland's steel. I
also show you specimens of cold bending:
Tensile Elong. Fractured Broke Fall Tons. in. 5" Bend. Blows. Blows.
In. G = 30.9 27½ p. c. Good 59 66 12 H = 29.3 30 p. c. Good 66 90 12
I = 28.9 28.9 p. c. Good 53 68 12
I think all of the above tests show that this material, when carefully
made and treated with sufficient mechanical work on forging down
from the ingot, is suitable up to 34 tons for crank shafts; how much
higher it would be desirable to go is a question of superior excellence
in material and manufacture resting with the makers. I would, however,
remark that no allowance has been made by the Board of Trade or
Lloyds for the excellence of this material above that of iron. I was
interested to know how the material in the best iron shafts would stand
this fatigue test compared with steel, and had some specimens of same
dimensions cut out of iron shafts. The following are the results: Best
iron, three good qualities, rolled into flat bars, cut and made into 4½
cwt. blooms.
J = 18.6 24.3 p. c. Good 17 18 12
Made of best double rolled scrap, 4½ cwt. blooms.
K = 22 32½ p. c. Good 21 32 12
You will see from these results that steel stood this fatigue test,
Vickers' 73 per cent. and Steel Co.'s 68 per cent., better than iron of the
best quality for crank shafts; and I am of opinion that so long as we use
such material as these for crank shafts, along with the present rules, and
give ample bearing surface, there will be few broken shafts to record.
I omitted to mention that built shafts, both of steel and iron, of large
diameter, are now in general use, and with the excellent machines, and
under special mechanics, are built up of five separate pieces in such a
rigid manner that they possess all the solidity necessary for a crank
shaft. The forgings of iron and steel being much smaller are capable of
more careful treatment in the process of manufacture. These shafts, for
large mail steamers, when coupled up, are 35 feet long, and weigh 45
tons. They require to be carefully coupled, some makers finishing the
bearings in the lathe, others depend on the excellence of their work in
each piece, and finish each complete. To insure the correct centering of
these large shafts, I have had 6 in. dia. recesses ¾ inch deep turned out
of each coupling to one gauge and made to fit one disk. Duplicate disks
are then fitted in each coupling, and the centering is preserved, and
should a spare piece be ever required, there is no trouble to couple
correctly on board the steamer.
The propeller shaft is generally made of iron, and if made not less than
the Board of Trade rules as regards diameter, of the best iron, and the
gun metal liners carefully fitted, they have given little trouble; the
principal trouble has arisen from defective fitting of the propeller boss.
This shaft working in sea water, though running in lignum vitæ
bearings, has a considerable wear down at the outer bearings in four or
five years, and the shaft gets out of line. This wear has been lessened
considerably by fitting the wood so that the grain is endway to the shaft,
and with sufficient bearing surface these bearings have not
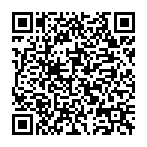
Continue reading on your phone by scaning this QR Code
Tip: The current page has been bookmarked automatically. If you wish to continue reading later, just open the
Dertz Homepage, and click on the 'continue reading' link at the bottom of the page.