overcome.
Some of these early instruments were not even provided with dampers for stopping the tone when the key was released; consequently, when a number of keys were struck in succession, the tone continued from all, so long as the strings would vibrate. The strings and sound-board being very light, the sustaining qualities were meager compared to those of the modern piano; consequently the dampers were not so much missed as they would be if removed from a modern upright or grand, which would surely render them unfit for use.
In the first attempts at piano building, the difficulties to be overcome may be enumerated as follows: The frames were not strong enough to resist the tension of the strings; they were made almost entirely of wood which yields to the pull of the strings and is subject to climatic changes; the scale was very imperfect, that is, the length, tension and weight of the strings were not properly proportioned, the result being a different quality of tone from different portions of the keyboard; the actions were either heavy and imperfect, or too light to produce sufficient vibration; the proper point upon the strings for the hammers to strike and for the dampers to bear had not yet been ascertained; the preparation and seasoning of the wood for the different parts of the instrument had not received sufficient attention.
One cannot conceive how difficult it is to produce something that has never existed, until he tries. The requirements necessary to such results as are obtainable from the modern piano are numerous and rigid and the result of many costly experiments.
Probably the most important essential in piano building is the production of a frame of such strength and stability that the enormous tension of the strings is completely resisted in all parts of the scale. In many of the cheaper pianos of this day, the lack of this essential manifests itself in an annoying degree to the piano tuner. In tuning, the workman "brings up" his temperament in the middle of the instrument; in most cases the temperament stands all right. He next tunes the treble, then the bass; after doing his work perfectly he will often find that the treble fell somewhat while he was bringing up the bass; or, in a few cases, he may find that the treble sharpened, thus showing that there was yielding of the frame. Of course, this defect might be overcome by using an extremely heavy metal plate and wooden frame; but the commercial side of the question, in this day, calls for lightness in the instrument as a check to the expense of production, and, consequently, pianos that are "made to sell" are often much too light to fulfil this requirement.
In the upright piano, the back frame of wood is first made; at the top of this is the pin-block, sometimes called the wrest-plank. This is composed of several layers of wood firmly glued together with the grain running in different directions to prevent splitting and warping. Into this plank the tuning pins are driven. The sound-board is fitted firmly into this frame of wood below the pin-block.
Next, the strong metal plate is secured to the frame by large bolts and screws. Openings are left in the plate for the bridges, which project from the sound-board beyond the metal plate; also for the tuning pins, action bracket bolts, etc.
At the lower end of the plate, and just below the bridges,[B] the hitchpins are driven firmly into holes drilled to receive them. Their purpose is to support the lower ends of the strings. The bass strings are separate, and each has a loop with which to fasten it to the hitchpin. In the treble, one piece of wire forms two strings; the two ends are secured to the tuning pins above, and the string is simply brought around the hitchpin. The bridges communicating with the sound-board are at the lower end of the sound-board. Notice, there is a portion of the length of each string between the bridge and the hitchpin.
[B] There are two sections of the lower bridge, one for the treble and one for the overstrung bass.
[Illustration]
At the upper end of the strings, a "bearing-bar," situated between the tuning pins and upper bridge, is attached to the pin-block by screws which draw it inward; its function is to hold the strings firmly in position. You will notice that the lengths of the strings, above the bearing-bar, vary considerably, even in the three strings comprising the unison. (We will speak of the effect of this in tuning, farther on.)
After that portion of the case is completed which forms the key-bed or action frame, we are ready to set in the
ACTION.
By this is meant the keys and all those intricate parts which convey the motion of the
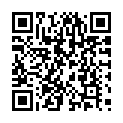
Continue reading on your phone by scaning this QR Code
Tip: The current page has been bookmarked automatically. If you wish to continue reading later, just open the
Dertz Homepage, and click on the 'continue reading' link at the bottom of the page.