rework of the faulty items???
- Do you know precisely how each will be affected???
- Do the supervisors and direct workers of those work units and at each workstation understand the problem and what is expected of them? ?? - Have you ascertained which work units and workstations can be by-passed during the fix to minimize disruption to routine operations and production and thereby reduce cumulative adverse effects???
- Will the fix make it necessary to???
- Realign workspace???
- Move shop equipment???
- Modify tools and equipment???
- Fabricate jigs and special holding devices???
- Redesign parts and assemblies???
- Revise quality assurance standards and procedures, and production practices??? - Retrain people???
- Reschedule and reprogram other work???
- Modify contracts with suppliers and customers???
- Does fixing the mistake call for a documented Corrective Action Plan, commitment of significant resources, and detailed production scheduling???
- Can the corrective action taken as a result of this error be applied to future designs, and management policies and practices, and for production system improvements elsewhere in your plant???
- Has this experience given you ideas to improve your operations???
- Have you documented what you learned, tested them, and injected the results into your plant practices???
#
A corrective action plan is forward-looking: it specifies the action steps and their sequence for fixing the defective items and the changes that need to be integrated into the product line management system. It is positive-oriented and concentrates on the fix to the exclusion of looking back for who did what and why. The investigative and blame job is not planning and belongs to another group.??
As a manager, supervisor and leader, take that extra step that prevents the same or comparable mistakes from happening. What really caused the problem? What can and should be done about it? Is a significant change needed in tools, equipment, or materials? Should the shop layout be changed? Do workers need additional training? Are product inspection and quality assurance skills, methodologies and standards tight enough? Are you using the right vendors? The mistake and its underlying causes that were resolved at one shop location could provide opportunities for a significant technical or management improvement throughout the plant. Have you and your staff thought through the possibility of recurrence, and have you done something constructive to preclude its happening?
MEMOIR: THE FIRST LINE SUPERVISOR INSPECTS THE WORK UNIT
I drafted this procedure in the 1960s when I was a management analyst on the staff of an Inspector General at an Air Force logistics depot in California. The concept, and its implementation, was presented at seminars attended by the activity's crew chiefs and supervisors.
The concept and process lends itself to computerization in sequencing steps in planning, committing and pre-positioning appropriate tools, inspection equipment, periodic servicing and replacing materials, parts and lubes, in conducting follow up, and as a guide for training and motivating supervisors, crew chiefs, and participants in Regional Occupational Programs generally.
#
A first-line supervisor's inspection of his/her work unit will vary according to the unit's mission, layout, equipment, and product or service. The information may interest students who are training for a skill or vocation as a career, developing their managerial skills, or who are preparing to establish themselves in a business. It may also be useful to businessmen and women who are refining their supervisory training courses and the quality of their production environment. The objective is an optimal work environment with employee safety and satisfaction.
The supervisory inspection is an on-site, searching examination of the operating level of a work unit, its internal environment and its operating systems. The inspection is conducted by the unit supervisor who is directly responsible for the work unit or, where special skills are required, by technicians or administrators who are under the unit supervisor's surveillance during the inspection.
The inspection checks for compliance with the company's and the supervisor's policies and accepted work practices. In the process, deficiencies that need early attention are identified and acted upon.??
Examples of where expeditious actions might be needed are those that would prevent damage to or failures in product, equipment and material, reduce or eliminate a potential safety hazard, or modify an environmental condition or operational practice to meet a new requirement. The inspection technique draws upon, and enhances, the experience of managers, supervisors and technicians at all levels. It also provides higher-level superiors with a means to evaluate a subordinate supervisor's capabilities and judgment.
The objectives of a supervisory inspection are to:
- detect existing and potential errors as close to the points of origin as possible so as to protect property;
- verify adequacy of work unit procedures and controls; and ensure compliance with safety directives.
The indirect benefits of the inspection are opportunities to:
- observe conditions that have diagnostic value, such as identifying barriers to mission accomplishment and operational effectiveness;
- assess consequences of changes brought about by new policies, procedures, and corrective actions for previously noted inadequacies;
-
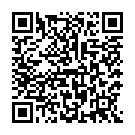
Continue reading on your phone by scaning this QR Code
Tip: The current page has been bookmarked automatically. If you wish to continue reading later, just open the
Dertz Homepage, and click on the 'continue reading' link at the bottom of the page.