the shipments be off-loaded???
- Do you know the effect of a stop shipment order on the customers/consumers who are scheduled to receive the items???
- Do they have sufficient stocks on hand that do not contain the error to tide them over the re-work period?
- Should you permit shipments to continue and then dispatch technicians to replace or repair the defective parts at the customer's/consumer's holding facility or maintenance and/or operating site???
- If the defective items have been shipped to distributors and from them to ultimate consumers, can you identify all shipments that incorporate the production error by customer/consumer, shipping order number, method/date/time of shipment, and any other means that will assist the recipients to locate and, if necessary, segregate defective from useable stocks in their warehouses, dealers' stocks and in (consumer's) possession???
- Have you issued instructions to cover the situation???
- Have you confirmed that your instructions were followed???
- Based on your analysis to this point, should the recipients of items containing the defective part be notified???
- If notification is to be made, have you issued instructions to do so and are your instructions clearly understood???
- Have you and your legal advisors reviewed the notification for adequacy, including legal and contractual implications???
- Do notification procedures include recording date/time/method of notification and names of individuals originating and receiving the communications???
- Are you certain the notification was received and understood by the intended recipient???
- If you have imposed a work stoppage on the affected items and stopped further shipments, do you know your shipping commitments for the next 24, 48 and 72 hours???
- Should the recipients for those shipping commitments (preceding question) be notified of the delays, lead time until the situation can be clarified, and when a new shipping date will be provided? Was this step followed up with the notification of a new shipping date? ?? - If the faulty items are to be recalled to the plant, can shipments in the transportation pipeline be diverted back???
- If they can be returned, were instructions to that effect issued, and has receiving function prepared paperwork for the non-routine receipts and for their segregated storage until shop processing can be accomplished???
- Should you arrange with your customers for them to rework the defective items in their service support shops or contractually???
- Would it be more practical for you to send your technicians to do the rework on site, considering your customer's resources (time, special tools, equipment, replacement parts, materials, skills, calibration), the economics of the situation, and your company's reputation???
- Have you identified and analyzed your options for each location where the fix will be made? Have you listed them and evaluated their interactions???
- Have you evaluated the effects of your decision to fix or not fix?
IMPLEMENTING THE FIX
- Identify the factors and decisions that would bear upon the corrective action process for that particular manufacturing mistake.??
- List, in check-list form, the considerations and options that would enhance management's understanding of the exact nature and significance of the mistake and its effects on the pipeline, wholesalers, other points in the transport/warehousing system, consumers, vendors of components, and you, the manufacturer.
- Review relevant policies and procedures; activate the plant's corrective actions task group; designate and appoint a task group leader; prepare a comprehensive corrective action plan; select subordinate (function) leaders, production staff and line crew chiefs, technicians, and line workers; design and procure or manufacture replacement parts; marshal tools, equipment and other resources; designate and commit work stations, and implement the approved 'corrective action plan.'
- Notify and make/secure commitments to/from concerned entities that are located outside of the plant. Integrate the fix and what was learned from the experience, into the organization's management, engineering (RDT&E), procurement, production and supporting management systems to preclude the mistake's recurrence.
- Have you considered the demands that will be made on and the adequacy and availability of your:??
- Plant facilities (structural and environmental)???
- Finances/accounting? ?? - Energy sources???
- Communications systems???
- Transportation???
- Public relations and marketing? ?? - Shop equipment and tools available and tested???
- Supplies and long-lead acquisition time materials???
- Data? ?? - People (skills, training, safety, working hours, etc.)?
- Resources in other functions that will be involved???
- Can the faulty assemblies be processed economically for tear down to get at and remove the defective part and then to return the remaining (good) parts to your routine production system without disrupting the product line???
- If not, do you need a special, one-time production task group for the defective sub-assemblies to do the tear down, repair, and re-assembly job???
- If, after teardown, the parts (minus the defective item) can be returned to routine production, have you identified the points along the production system where each good assembly and/or component can be re-checked and reused?
- Have you identified all the work units and workstations that will be directly affected by the
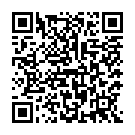
Continue reading on your phone by scaning this QR Code
Tip: The current page has been bookmarked automatically. If you wish to continue reading later, just open the
Dertz Homepage, and click on the 'continue reading' link at the bottom of the page.