and the fix relates to a manufactured
product, the options (check list elements) might be applicable or
adaptable to public and private sector construction, health care, support
and services, general administration, and other functions and processes,
as appropriate to the reader's interests.
The coverage given here is intentionally general; no two manufacturers,
institutions, service entities, down to their first line work sites are
exactly alike in their tasks, equipment layout, skills, environment,
human factors, staff and supervisory personalities, etc. The interaction
of all of these factors, within and outside the work unit, affects how an
approved fix is installed and how it works out. The planning for and
integration of a fix (the clarity of procedures and sequencing of who
does what and when) takes into account the uniqueness of the problem
and the work site or station.
#
Mistakes challenge a leader's sense of order. Timely and effective
corrective action may be vital to the safety of a product, the welfare of
consumers, and the stability of the organization in which the mistake
occurred.
Each product, its design/production system and support functions have
unique characteristics. Fixing a mistake that results from the manner in
which these and other unique characteristics are organized or operate
needs to consider all of the elements that contributed to the
circumstances and environment within which the mistake occurred. The
most immediate task, beyond safety to life inside and outside the
workplace, is to organize available skills and resources so as to
pinpoint the cause of the mistake; determine, specify, and correlate the
steps of a corrective action, implement the fix, and reduce the
likelihood of the mistake's recurrence.
The Checklist is a Tool of the Corrective Action Team
Several thousand units of a newly designed device, manufactured in
one plant, were found to have a defective part. The first-level assembly,
into which the defective part was initially installed at a product-line
workstation, had then moved on to subsequent workstations where they
were incorporated into higher-level assemblies. Eventually, the
assembly, with the defective part still installed, made its way through
final assembly.Â
Several hundred completed devices (the end items), incorporating the
defective part, were in post-final-assembly. They were in holding areas,
on their way to or already in the shipping department's temporary
storage warehouse, or had been loaded on to shipping vans of which the
drivers were finishing up paper work to depart for destinations
throughout the country to deliver the finished devices to wholesalers,
distributors, or ultimate retailer. Another several hundred devices had
previously departed the plant and were in the transportation pipeline, at
dealers and retailers, or in the possession of consumers. Each
completed device (the manufacturer's end item) and its outer shipping
container had its own visible serial-number identification.
ANALYSIS
- What was the mistake?Â
- Did a part break, crack, bend or misalign?Â
- Was a circuit incomplete?Â
- Were incorrect materials used or dimensions applied?Â
- What really happened?Â
- Have you and concerned supervisors and staff examined physical
evidence of the mistake?Â
- Do you know where in the plant the mistake actually occurred?Â
- Have you pinpointed and brought to the attention of the management
and production staff the specific work unit and workstation where the
error was first noticed?Â
- Did you backtrack along the production line to the workstation and
employee where the mistake was made?Â
- Did you track the mistake forward along the production system to
ascertain the extent to which the fault was included in higher
assemblies?
- Did you stop the work operation that was creating the mistake?Â
- Should you institute a work stoppage?Â
- Did you identify the people, skills, materials, tools, equipment, and
data in all related programs, work practices and procedures that caused
or contributed to the mistake?Â
- Do you know which were directly responsible?Â
- Do you know which were indirect contributors?Â
- Do you know how they became part of the approved design, vendor
support, and/or production process?Â
- Have you identified where (functions, work units) and with whom
(supervisors) the accountability lays?Â
- Must you correct the mistake on the completed/shipped end items or
on items on which rework would be economically or technologically
unprofitable or impractical? In answering this question have you
considered?Â
- Safe and economical use of the final product by the ultimate
consumer?Â
- Acceptability under established quality standards and the governing
technical specifications and contracts?Â
- The effect on the part's and the end item's service life?Â
- Maintainability and accessibility of the part in the end item during
normal usage?Â
- The effect on the cost of operating the end item, and reducing the time
between maintenance inspections, parts replacements,
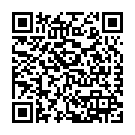
Continue reading on your phone by scaning this QR Code
Tip: The current page has been bookmarked automatically. If you wish to continue reading later, just open the
Dertz Homepage, and click on the 'continue reading' link at the bottom of the page.