older adults generally have technical
and professional skills, are mature-minded, and form a constantly
replenished technological and cultural resource. Their capabilities and
perceptivity are the result of many years of hands-on, supervisory or
management experience in a trade or profession, tempered by practical
interactive human relations. It is characteristic in almost all species that
survive by more than instinct that the experienced pass their knowledge
along to the young whenever the time is right for them to do so. The
urge to pass knowledge forward to a succeeding generation is ingrained
as deeply as instinct. Older adults, as grandparents or otherwise, will
always do what older adults do best: working with, guiding, and
mentoring youth. Fixing mistakes, learning from the process, and
passing forward what was learned is inherent in survival of the species.
I presented an earlier version of this memoir's contents as a United
States Small Business Administration 'Management Aid for Small
Manufacturers,' number 242 'Fixing Production Mistakes' published in
March 1979. I've reworked the text since and occasionally email copies
in response to requests. The checklist may be useful in Regional
Occupational Programs (ROP) and supervisory and crew chief training.
Correcting a mistake starts with understanding what went wrong.
One rarely reads a newspaper without noting a report about a foodstuff,
medication, or device on the market or in use for its intended purpose,
was recalled by the manufacturer. Whatever it is, it was not doing the
task for which it was intended or designed, and continued use might
risk life, quality of life, or property.
For example, a national business newspaper reported that a motor
vehicle manufacturer was recalling more that 100,000 vehicles of
various models. The reason was faulty secondary door latches, and an
electrical harness support device in which an electrical short might
occur, possibly causing a fire.
Faulty manufacture, construction, inspection or training in any function
concerned with manufacturing a product or providing a service all too
often have serious consequences.
What follows is based on my Inspector General experiences in tracking
compliance with 'corrective action' commitments for mistakes and
deficiencies at a major military industrial facility. The errors had been
noted and reported on by higher headquarters and private sector
technical and management inspection teams.Â
Management and technical inspection and other oversight methods
have changed significantly with computerization. Nevertheless,
mistakes still happen, at times the same as before computerization, and
they continue to happen. Management oversight and controls over
fixing mistakes and their causes need to keep abreast with the analyses
of a mistake's occurrence, its complexity and safety implications, and
other immediate and ripple effects of the event. Useful ideas on
preventing and fixing mistakes need to cross feed across all elements
and levels of our society. Ignoring cross feed escalates the
unconscionable waste of the nation's and the world's resources and
could increase needless loss of lives and property.Â
In my work as an Inspector General's analyst at a major Air Force
logistics base I prepared a checklist of elements to be considered in
planning corrective actions for mistakes in various supply and
maintenance shops. I discussed and distributed the checklist during
seminars that I conducted on the subject for crew chiefs and first and
second line supervisors. My hope was that the check list would also be
useful to managers, line-and-staff supervisors, procedures specialists,
product-line workers and crew chiefs, and teachers and students at
vocational and other schools of public and private sector enterprises
and institutions. The checklist was subsequently published by the Small
Business Administration as Management Aid MA242 Fixing
Production Mistakes and widely distributed to industry, libraries and
vocational schools.Â
#
The checklist suggests a few of the many steps and considerations that
go into preparing for and following through on a 'fix' for a mistake in
manufacturing, support, services, or other operations in the work place.
Record keeping has improved with the computer; but it's still up to
people to think the problem through, arrive at resolutions, and ensure
that the fix is implemented and effective.
The options are shown in checklist form and any one of them may or
may not apply to a specific situation in a shop or office. The fact is that
any one mistake, and its causes and effects, as a collection of distinct
but interacting events, is unique and needs to be addressed in that
context. There is no general all-purpose after-the-fact corrective action
plan, nevertheless, generalized contingency planning, for example, in
the form of a documented Practice on getting organized around the
corrective action job would be useful. The objective is to (1) fix the
mistake, (2) keep it from happening again, and (3) integrate what was
learned from the experience into the organization's existing engineering
and other production functions, training and other management
systems.
Although the mistake (event)
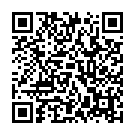
Continue reading on your phone by scaning this QR Code
Tip: The current page has been bookmarked automatically. If you wish to continue reading later, just open the
Dertz Homepage, and click on the 'continue reading' link at the bottom of the page.