control 133
5.9 Filling principles 133 5.9.1 Gravity ller 135
5.9.2 Counter-pressure ller 137
5.10 Nitrogen 142
Further reading 142
6 Modern filling systems for carbonated soft drinks 144
Andrew Wilson and John Medling
6.1 Introduction 144
6.2 Modern carbonation systems 147
6.3 Counter-pressure llers 149 6.3.1 Operation 149
6.3.2 Level lling 154
6.4 Glass bottle lling 156 6.4.1 Operation 156
6.4.2 Bottle burst protection 159
6.5 PET (polyethylene terephthalate) bottle lling 161 6.5.1 Operation 161
6.5.2 Size changing 162
6.6 Can lling 166 6.6.1 The volumetric can (VOC) ller 166
6.6.2 System expansion – the VOC-C can ller 168
6.6.3 Product level- and pressure-control system in a free-standing product tank 170
6.6.3.1 Level control 170
6.6.3.2 Filling pressure control 170
6.6.4 Procedural steps of the lling cycle 170 6.6.4.1 Flushing phase I 171
6.6.4.2 Flushing phase II 171
Steen: “fm” — 2006/4/27 — 18:30 — page ix — #9
CONTENTSix
6.6.4.3 Pressurising 171
6.6.4.4 Filling 171
6.6.4.5 Snifting 172
6.6.4.6 Recharging the metering chamber 172
6.6.4.7 CIP cleaning 173
6.7 Other ller options 174
6.8 Clean-in-place 175
6.9 Filler hygienic design 177
6.10 Conclusions 178
7 Bottle design and manufacture and related packaging 181
David Syrett
7.1 Introduction – the objectives of packaging 181
7.2 Glass 182 7.2.1 History of glass making 182
7.2.2 Bottle supplier identi cation marks 184
7.2.3 Bottle design and headspace considerations 184
7.2.4 Glass bottle manufacturing processes 185 7.2.4.1 The melting process 185
7.2.4.2 Glass bottle forming 187
7.2.5 Glass quality faults 189 7.2.5.1 Critical defects 189
7.2.5.2 Major defects 189
7.2.5.3 Minor defects 190
7.2.6 Single and multiple trip bottles 192
7.2.7 Lightweighting 193
7.2.8 Recycling 194
7.3 Plastic bottles 194 7.3.1 Introduction – advantages and limitations 194 7.3.1.1 Advantages 194
7.3.1.2 Limitations 195
7.3.2 Polyethylene terephthalate 195
7.3.3 History 195
7.3.4 PET bottles today 196 7.3.4.1 Preforms 196
7.3.4.2 Bottle blowing 196
7.3.5 Multilayer and barrier coating 198
7.3.6 Carbonation loss 198
7.3.7 Permeability of polymers 198
7.3.8 Recycling methods 200
7.4 Closures for carbonated soft drinks 200 7.4.1 Introduction 200
7.4.2 Headspace pressure 201
Steen: “fm” — 2006/4/27 — 18:30 — pagex—#10
xCONTENTS
7.4.3 Roll on metal closures 202
7.4.4 Plastic closures 202
7.4.5 Development of the PET bottle nish 203
7.4.6 Crown corks (pry off/twist off) 205
7.4.7 Other closures (vacuum lug/rip off) 205
7.5 Cans and ends 206
7.5.1 Introduction 206
7.5.2 The can making process 206
7.5.2.1 Front-end processes 206
7.5.2.2 Decoration processes 207
7.5.2.3 Back-end processes 207
7.5.3 Graphics decoration 208
7.5.4 Ends 208
7.5.5 The double seam 208
7.5.6 Can end stress corrosion 208
7.6 Labels and labelling 209
7.6.1 Introduction 209
7.6.2 Paper manufacturing 210
7.6.3 Labelling 210
7.6.4 Patch labellers 212
7.6.5 Wraparound labellers 213
7.6.6 Sleeving 215
7.6.7 Labelling in production 215
7.6.8 Date coding (ink jet/laser) 216
7.7 Future trends – putting it all together 216
Further reading 217
8 Secondary packaging considerations 218
David Rose
8.1 Introduction 218
8.2 Requirements of the supply chain 219
8.2.1 Overview 219
8.2.2 Major multiple 221
8.2.2.1 Pallet receipt 221
8.2.2.2 Pallet breakdown and load picking 221
8.2.2.3 Bar codes 221
8.2.2.4 Store delivery 222
8.2.3 Cash & Carry 224
8.2.3.1 Pallet breakdown and load picking 224
8.2.3.2 Pack graphics 224
8.2.3.3 Bar codes 224
8.2.4 Bulk break 224
8.2.5 Poor packs – no sale? 225
Steen: “fm” — 2006/4/27 — 18:30 — page xi — #11
CONTENTSxi
8.2.6 Material – performance versus speci cation 225
8.3 Pack styles 227
8.3.1 Shrink wrap 227
8.3.2 Trade ready display unit (TRDU) 228
8.3.3 Shelf ready packing 229
8.3.4 Returnable crate 231
8.4 Shrink lm production 231
8.4.1 Film considerations 231
8.4.2 Shrink wrap packers 233
8.4.3 Printed shrink wrap 234
8.5 Corrugated breboard 239
8.5.1 Speci cations 239
8.5.2 Corrugated board manufacture 240
8.6 Stretch wrap 240
8.6.1 Material 240
8.6.2 Stretch wrapping systems 244
8.6.3 Pallet wrapping 247
8.7 Pallets and pallet stacking 248
8.7.1 Pallets 248
8.7.2 Pallet stacking 248
8.8 Case and pallet labelling 249
8.9 Getting it wrong 253
8.10 Developments and testing 257
8.11 Putting it all together 258
9 Production systems 259
David Steen
9.1 Introduction 259
9.2 Philosophy of line layouts 259
9.3 Glass bottle lling lines 260
9.4 Can lling lines 267
9.5 PET bottle lling lines 268
9.6 Conveying systems 270
9.7 Inspection systems 272
9.8 Breakdown characteristics 274
9.9 Line control and management systems 277
9.10 Complete factory layouts 280
9.11 Buildings 283
9.12 Performance measurement and benchmarking 285
9.13 Future trends 288
Further reading 289
Steen: “fm” — 2006/4/27 — 18:30 — page xii — #12
xiiCONTENTS
10 Production planning and distribution 290
Philip A. Wood
10.1 Introduction 290
10.2 Supply chain principles 291
10.2.1 Make versus buy 292
10.2.2 Make to order or make to stock 293
10.2.3 Purchasing 294
10.2.4 The soft drinks supply chain 296
10.2.5 The bullwhip effect 298
10.3 Forecasting 299
10.3.1 Forecast breakdown or types 300
10.3.2 Forecast preparation and accuracy 301
10.4 Planning 301
10.4.1 The planning and order cycle 301
10.4.2 Central or local planning 304
10.5 Warehousing 307
10.5.1 Environment 314
10.5.2 Stock control 314
10.6 Transport and legislation 315
10.7 Measuring supply chain performance 316
10.7.1 Service 316
10.7.2 Costs 317
10.7.3 People 317
10.7.4 Resources 317
10.8 Conclusions and future developments 317
Bibliography 318
11 Quality, environment and food safety systems 319
Ray Helliwell
11.1 Why have systems? 319
11.1.1 De nitions 319
11.1.2 Space shuttle fails 319
11.1.3 Risk management 320
11.1.4 A solution? 320
11.2 Management control 321
11.2.1 Constraints –
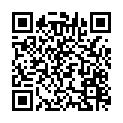
Continue reading on your phone by scaning this QR Code
Tip: The current page has been bookmarked automatically. If you wish to continue reading later, just open the
Dertz Homepage, and click on the 'continue reading' link at the bottom of the page.