to the engraver, though much more for bank-notes and large pieces of work than for postage stamps. These are called ruling machines, medallion rulers, cycloidal and geometric lathes. Ruling machines are used to make the backgrounds of portraits, the shadings of letters and similar work.
[Illustration: Coin Stamp, "New South Wales", 5 shillings]
Here is a very pretty example of ruling, in the so-called "coin" stamp of New South Wales. These machines rule either straight or curved lines. They can be adjusted to rule several thousand lines to an inch, but that is only done for microscopical work, not for engraving. The general principle of a medallion ruling machine is a rod, fixed on a pivot, at one end of which is a pin which is drawn across a medallion, while at the other end a graving point traces a corresponding line on the steel. The large stamps issued in the United States in 1865, for the payment of postage on newspapers and periodicals, are examples of this work.
Cycloidal ruling in its simplest form resembles a series of loops. It is produced by a fixed point which is held against a plate while the latter is moved in a circle and, at the same time, forward. By altering the size of the circle and the speed of the forward movement a great variety of results are obtained. By cutting one series of loops over another, lace-like effects are produced. The process is still further varied by the use of eccentrics.
[Illustration: Ruling Patterns]
The geometric lathe is a most delicate and complicated machine. By means of elaborate attachments very involved and eccentric motions are given to the plate under the graving point and extremely complicated and beautiful designs are produced. I think we are all familiar with these from the examples on our national currency. Geometric lathework was used on a number of the United States stamps of the issue of 1861 and also on the $5,000 revenue stamp. The work of this machine is regarded as a great safeguard against counterfeiting. The most skillful engraver would have difficulty in imitating the simplest designs produced by it. The machines are too expensive to be obtained by anyone but a government or a great banknote company and there are very few men who thoroughly understand operating them. A turn of a screw or a variation of a single cog will change the result entirely. Finally the work of the lathe is often reversed, so that the line which is cut by the graver and should print in color prints white, and vice versa. It would not be possible to imitate this by hand engraving.
Printing from line-engraved plates is largely done by hand presses. The ink used is very thick. When black it is made of finely pulverized carbon, mixed with oil. Colored inks are composed of zinc white and dry colors, ground in oil. The colors are animal, vegetable or mineral. The latter cause the plates to wear out rapidly. Green is an especially destructive color. In recent years aniline colors have been largely employed. They afford an elaborate range of shades and color combinations which are most puzzling to describe. Soluble inks are much used by the leading English firm of stamp printers. They are very sensitive to water and are regarded as one of the best preventatives of the cleaning of used stamps. Beautiful results are obtained by printing stamps in two colors. Of course, this necessitates the use of two plates for each design. This also gives rise to some interesting varieties, caused by one part of the design being printed upside down. Such oddities are scarce and are highly valued by philatelists.
When a plate is to be printed from, it is first warmed, then the ink is applied and rubbed into the lines with a pad. The surface of the plate is wiped off with a cloth, then with the hand and lastly, polished with whiting. A sheet of dampened paper is next laid on the plate and the whole is passed under the roller of a press, which forces the paper into the lines of the plate, where it takes up the ink. When the plate is deeply engraved the ink seems to stand up from the surface of the paper in ridges and some times we find corresponding depressions on the backs of the stamps. The sheets are then dried, gummed and dried again. They are now so much curled and wrinkled that they are placed between sheets of bristol board and subjected to hydraulic pressure of several hundred tons which effectively straightens them out.
The second process of printing from metallic plates is called typography. The plates for this process are the exact reverse of those engraved in taille douce. Instead of the design being cut into the plate,
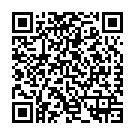
Continue reading on your phone by scaning this QR Code
Tip: The current page has been bookmarked automatically. If you wish to continue reading later, just open the
Dertz Homepage, and click on the 'continue reading' link at the bottom of the page.