Near Marseilles, France (1866).]
This form of mechanism, therefore, earned a bad name and was making
little advance, if not actually being abandoned, when a skilled
electrician, Robert Hope-Jones, entered the field about 1886. Knowing
little of organs and nothing of previous attempts to utilize electricity for
this service, he made with his own hands and some unskilled assistance
furnished by members of his voluntary choir, the first movable
console,[4] stop-keys, double touch, suitable bass, etc., and an electric
action that created a sensation throughout the organ world. In this
action the "pneumatic blow" was for the first time attained and an
attack and repetition secured in advance of anything thought possible at
that time, in connection with the organ or the pianoforte.
Hope-Jones introduced the round wire contact which secures the ideally
perfect "nibbing points," and he makes these wires of dissimilar
non-corrosive metals (gold and platinum).
He replaced previous rule-of-thumb methods by scientific calculation,
recognized the value of low voltage, good insulation and the avoidance
of self-induction, with the result that the electro-pneumatic action has
become (when properly made) as reliable as the tracker or pneumatic
lever mechanism.
DESCRIPTION OF THE ELECTRIC ACTION.
The electric action consists substantially of a small bellows like the
pneumatic lever, but instead of the valve admitting the wind to operate
it being moved by a tracker leading from the key, it is opened by an
electro-magnet, energized by a contact in the keyboard and connected
therewith by a wire which, of course, may be of any desired length. We
illustrate one form of action invented and used by Hope-Jones.[5]
Within the organ, the wires from the other end of the cable are attached
to small magnets specially wound so that no spark results when the
electric contact at the key is broken. This magnet attracts a thin disc of
iron about 1/4 inch in diameter, (held up by a high wind pressure from
underneath) and draws it downward through a space of less than 1/100
of an inch.
The working is as follows: The box A is connected with the organ
bellows and so (immediately the wind is put into the organ) is filled
with air under pressure, which passes upwards between the poles of the
magnet N. Lifting the small iron disc L it finds its way through the
passage L into the small motor M, thus allowing the movable portion of
the motor M to remain in its lower position, the pallet C|1| being closed
and the pallet C|2| being open. Under these conditions, the large motor
B collapses and the pull-down P (which is connected with the organ
pallet) rises.
[Illustration: Fig. 6. The Electro-Pneumatic Lever]
When a weak current of electricity is caused to circulate round the coils
of the electro-magnet N, the small armature disc J is drawn off the
valve-seat H on to the zinc plate K.
The compressed air from within the small motor M escapes by way of
the passage L, through the openings in the valve seat H into the
atmosphere. The compressed air in the box A then acts upon the
movable portion of the small motor M in such a manner that it is forced
upwards and caused (through the medium of the pull-wire E) to lift the
supply pallet C|1| and close the exhaust pallet C|2|, thus allowing
compressed air to rush from the box A into the motor B and so cause
this latter motor to open and (through the medium of the pull down P)
to pull the soundboard pallet from its seat and allow wind to pass into
the pipes.
[Illustration: Fig. 7. Valve and Valve Seat, Hope-Jones Electric Action]
The valve-seat H has formed on its lower surface two crescent shaped
long and narrow slits. A very slight movement of the armature disc J,
therefore, suffices to open to the full extent two long exhaust passages.
The movement of this disc is reduced to something less than the 1/100
part of an inch. It is, therefore, always very close to the poles of the
magnet, consequently a very faint impulse of electricity will suffice
(aided by gravity) to draw the disc off the valve-seat H. The zinc plate
K being in intimate contact with the iron poles of the magnet N,
protects the latter from rust by well-known electrical laws. All the parts
are made of metal, so that no change in the weather can affect their
relative positions. R is the point at which the large motor B is hinged. G
is a spring retaining cap in position; O the wires leading from the keys
and conveying the current to the magnet N; Q the removable side of the
box A.
Fig. 7 represents a larger view of the plate K in which the magnet poles
N
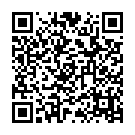
Continue reading on your phone by scaning this QR Code
Tip: The current page has been bookmarked automatically. If you wish to continue reading later, just open the
Dertz Homepage, and click on the 'continue reading' link at the bottom of the page.