CC, the break in the scale coming between GG
and FFF. Tenor C is an important note to remember. Here is where the
cheap builder came in again. He cut his stops short at tenor C, trusting
to the pedal pipes to cover the deficiency.
* * * * * *
[Illustration: PROSPER-ANTOINE MOITESSIER, INVENTOR OF
TUBULAR PNEUMATIC ACTION]
In the year 1845, Prosper-Antoine Moitessier, an organ-builder of
Montpellier, France, patented what he called "abrégé pneumatique," an
organ action in which all back-falls and rollers were replaced by tubes
operated by exhaust air. In 1850 he built with this action an organ of 42
speaking stops for the church of Notre Dame de la Dalbade at Toulouse.
This organ lasted 33 years. In 1866 Fermis, schoolmaster and village
organist of Hanterire, near Toulouse, improved on Moitessier's action
by combining tubes conveying compressed air with the Barker lever.
An organ was built on this system for the Paris Exhibition of 1867,
which came under the notice of Henry Willis, by which he was so
struck that he was stimulated to experiment and develop his action,
which culminated in the St. Paul's organ in 1872. (From article by Dr.
Gabriel Bédart in Musical Opinion, London, July, 1908.)
CHAPTER IV.
PNEUMATIC AND ELECTRO-PNEUMATIC ACTIONS.
Undoubtedly the first improvements to be named must be the
pneumatic and electro-pneumatic actions.
Without the use of these actions most of the advances we are about to
chronicle would not have been effected.
As before stated, Cavaillé-Coll and Willis worked as pioneers in
perfecting and in introducing the pneumatic action.
The pneumatic action used by Willis, Cavaillé-Coll and a score of other
builders leaves little to be desired. It is thoroughly reliable and, where
the keys are located close by the organ, is fairly prompt both in attack
and repetition. Many of the pneumatic actions made to-day, however,
are disappointing in these particulars.
TUBULAR PNEUMATICS.[1]
In the year 1872 Henry Willis built an organ for St. Paul's Cathedral,
London, which was divided in two portions, one on each side of the
junction of the Choir with the Dome at an elevation of about thirty feet
from the floor. The keyboards were placed inside one portion of the
instrument, and instead of carrying trackers down and under the floor
and up to the other side, as had hitherto been the custom in such cases,
he made the connection by means of tubes like gaspipes, and made a
pulse of wind travel down and across and up and into the pneumatic
levers controlling the pipes and stops. Sir John Stainer describes it as "a
triumph of mechanical skill." He was organist of St. Paul's for many
years and ought to know. This was all very well for a cathedral, where
". . . . the long-drawn aisles The melodious strains prolong"
but here is what the eminent English organist, W. T. Best, said about
tubular pneumatic action as applied to another organ used for concert
purposes: "It is a complete failure; you cannot play a triplet on the
Trumpet, and I consider it the most d----nable invention ever placed
inside an organ." Notwithstanding these drawbacks this action became
very fashionable after its demonstration at St. Paul's, and was used even
in small organs in preference to the Barker lever. One builder confessed
to the writer that he had suffered severe financial loss through installing
this action. After expending considerable time (and time is money) in
getting it to work right, the whole thing would be upset when the
sexton started up the heating apparatus. The writer is acquainted with
organs in New York City where these same conditions prevail.
The writer, however, will admit having seen some tubular actions
which were fairly satisfactory, one in particular in the factory of Alfred
Monk, London, England, where for demonstration purposes the tubes
were fifty feet long. Dr. Bédart informs us that Puget, the famous organ
builder of Toulouse, France, sets fifty feet as the limit of usefulness of
this action.
Henry Willis & Sons in their description of the organ in the Lady
Chapel of Liverpool Cathedral state that their action has been tested to
a repetition of 1,000 per minute, quicker than any human finger can
move. This is a square organ in one case, but we note they have
adopted the electric action for the great cathedral organ where the
distance of the pipes from the keys is too great for satisfactory
response.
In view of the wide use at present of this action we give a drawing and
description of its operation as patented and made by Mr. J. J. Binns, of
Bramley, Leeds, England. J. Matthews, in his "Handbook of the
Organ," says that this action is very good and free from drawbacks.
[Illustration: Fig. 5. Tubular Pneumatic Action]
The tubes,
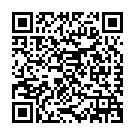
Continue reading on your phone by scaning this QR Code
Tip: The current page has been bookmarked automatically. If you wish to continue reading later, just open the
Dertz Homepage, and click on the 'continue reading' link at the bottom of the page.