stickful is emptied upon a galley. Then, when the page or the paper is "up," as the printers phrase it, the galleys are collected, and the foreman makes up the pages, article by article, as they come to us in the printed paper--the preliminary processes of printing proofs from the galleys, reading them by the proof readers, who mark the errors, and making the corrections by the compositors (each one correcting his own work), having been quietly and swiftly going on all the while. The page is made up on a portable slab of iron, upon which it is sent to the stereotyping room. There wet stereotyping paper, several sheets in thickness, is laid over the page, and this almost pulpy paper is rapidly and dexterously beaten evenly all over with stiff hair brushes until the soft paper is pressed down into all the interstices between the type; then this is covered with blankets and the whole is placed upon a steam chest, where it is subjected to heat and pressure until the wet paper becomes perfectly dry. Then, this dried and hardened paper, called a matrix, is placed in a circular mould, and melted stereotype metal is poured in and cooled, resulting in the circular plate, which is rapidly carried to the press room, clamped upon its cylinder, and when all the cylinders are filled, page by page in proper sequence, the pressman gives the signal, the burr and whirr begin, and men and scarcely less sentient machines enter upon their swift race for the early trains. As a matter of general interest it may be remarked that this whole process of stereotyping a page, from the time the type leaves the composing room until the plate is clamped upon the press, averages fifteen minutes, and that cases are upon record when the complex task has been accomplished in eleven minutes.
The paper is brought from the mill tightly rolled upon wooden or iron cores. Some presses take paper the narrow way of the paper, rolls for which average between 600 and 700 pounds. Others work upon paper of double the width of two pages, that is, four pages wide, and then the rolls are sometimes as wide as six feet, and have an average weight of 1,350 pounds. Each roll from which the New York Tribune is printed contains an unbroken sheet 23,000 feet (4-1/3 miles) long. A few hours before the paper is to be printed, an iron shaft having journal ends is passed through the core, the roll is placed in a frame where it may revolve, the end of the sheet is grasped by steel fingers and the roll is unwound at a speed of from 13 to 15 miles an hour, while a fan-like spray of water plays evenly across its width, so that the entire sheet is unrolled, dampened, for the better taking of the impression to be made upon it, and firmly rewound, all in twenty minutes. Each of these rolls will make about 7,600 copies of the Tribune.
When all is ready, paper and stereotyped pages in place, and all adjustments carefully attended to, the almost thinking machine starts at the pressman's touch, and with well nigh incredible speed prints, places sheet within sheet, pastes the parts together, cuts, folds and counts out the completed papers with an accuracy and constancy beyond the power of human eye and hand.
The printing press has held its own in the rapid advance of that wonderful evolution which, within the last half century, in every phase of thought and in every movement of material forces placed under the dominion of men, has almost made one of our years the equivalent of one of the old centuries. Within average recollection the single cylinder printing machine, run by hand or steam, and able under best conditions to print one side of a thousand sheets in one hour, was the marvel of mankind. In 1850, one such, that we started in an eastern Ohio town, drew such crowds of wondering on-lookers that we were obliged to bar the open doorway to keep them at a distance which would allow the astonishing thing to work at all.
To-day, in the United States alone, five millions of dollars are invested in the building of printing presses, many of which, by slightest violence to figure of speech, do think and speak. Inspiration was not wholly a thing of long-gone ages, for if ever men received into brain and worked out through hand the divine touch, then were Hoe, and Scott, and Campbell taught of God.
Under existing conditions newspapers of any importance, in the smaller cities, use one and sometimes two presses, capable of producing from 7,000 to 9,000 complete eight page papers each hour, each machine costing from $10,000 to $15,000. Papers of the
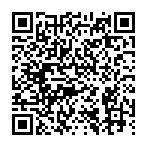
Continue reading on your phone by scaning this QR Code
Tip: The current page has been bookmarked automatically. If you wish to continue reading later, just open the
Dertz Homepage, and click on the 'continue reading' link at the bottom of the page.