and Egypt, from whence cotton is sent in bales, presses must have a long stroke; and unless they can be worked rapidly, a very considerable amount of plant is required to get through a moderate quantity of work. To meet the necessities of these countries, Mr. Watson has devised several forms of press in which not only is the table made to rise rapidly through the greater part of its stroke, but the rams are kept almost constantly in motion, so that the time occupied in filling the box with raw cotton and in placing the ties round the bales is not lost.
[Illustration: COMPOUND HYDRAULIC PRESS. FIGS. 1 and 2.]
We illustrate four forms of Mr. Watson's presses, Fig. 1 being an earlier construction, which, although very rapid at the date at which it was brought out, has been far surpassed in celerity by the arrangements shown in Figs. 3 to 8. It was introduced in 1873, and forty-three presses according to this design were sent to India by the makers, Messrs. Fawcett, Preston & Co., of Phoenix Foundry, Liverpool, between that year and 1880. Four presses of this kind are worked by one engine, having a cylinder 20 in. by 3 ft. stroke, and driving eighteen to twenty pumps of varying diameter and short stroke. The press has two long-stroke rams, LL, of small diameter, to compress the loose material, and two short-stroke rams, FF, of large diameter, to give the final squeeze. These two pairs of rams act alternately, the one pair being idle while the other is in operation. The lashing of the bale takes place while the larger rams are in action, the bale being supported on the grid, B, which is pushed under it through grooves formed in the press-head, S (Fig. 1). When the grid is in place the press-head can be lowered, and the box be filled, while the bale is receiving its final squeeze from the inverted rams above.
In Figs. 1 and 2 the press is shown in the position it would occupy if the bale, M, were just completed and ready to be pushed out, and the box, N, were full of material. The filling doors, CC, are shown turned back level with the floor, the main doors, AA, are open, as are also the end doors, KK, to admit the men to fasten up the bale. If water be admitted to the subsidiary cylinder, H, the head, G, and two rams, FF, will be raised, and then the bale, M, can be thrown out finished. All the doors are now closed and water admitted to the rams, LL. These immediately rise, pushing the contents of the box, N, before them, and compressing them until the table, S, reaches the level of the grid, B. At this moment the tappet rod, D, shuts off the water, and withdraws the bolt of the doors, AA, which fly open. The grid, B (Fig. 2), is then run through the grooves in the press-head, S, and the rams, LL, are allowed to descend ready for a baling cloth to be inserted through the doors, EE, and for the box, N, to be refilled. At the same time the head, G, comes down on to the bale and compresses it still further, while the men are at work lashing it. When the material is in hanks, like jute, the rams, LL, are lowered slowly, while a man standing inside the box, at about the level of the floor, packs the material neatly on the table.
These presses can be worked with great rapidity, the average output during a day varying from 21 to 28 bales an hour. The consumption of coal per bale is 9 lb. of Bengal coal, in value about ?d. The density of the cotton bales produced is about 45 lb. per cubic foot, 400 lb. measuring a little under 9 cubic feet for shipment. In the case of jute or jute roots, the same weight occupies 10 cubic feet on an average. But rapid as this press is in action, the necessities of recent business in India have called for still more expeditious working, and to meet this demand Mr. Watson produced his compound press, in which the economy of time is carried to its utmost development. By the addition of a second pair of long-stroke rams the output of the press has been trebled, being raised to 80 bales per hour. To effect this, there is one pair of powerful rams, as in the press just described, but two pairs of the long-stroke rams. Further, each pair of the small-diameter rams is fitted with two boxes, one of which is always being filled while the other is being pressed. The rams in rising compress the material into a small cell or box,
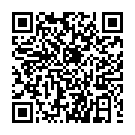
Continue reading on your phone by scaning this QR Code
Tip: The current page has been bookmarked automatically. If you wish to continue reading later, just open the
Dertz Homepage, and click on the 'continue reading' link at the bottom of the page.