metallic zinc do not give the real
composition of the zinc dust. For the determination of the metallic
components the material is digested with a solution of copper sulphate,
which dissolves zinc and cadmium; the liquid is filtered, acidified, and
decomposed with hydrogen sulphide, or treated with a solution of
ammonium carbonate. The use of cupric chloride is not advisable, as it
corrodes lead, and gives rise to the formation of soluble chloride of
lead, which complicates the separation of zinc from cadmium. The best
mode of operation is the following: Both copper sulphate and zinc dust
are weighed separately, the former is dissolved in water and the latter
introduced into the solution of copper sulphate in small portions until it
appears colorless. During the operation the vessel is freely shaken,
lumps are comminuted with a glass rod, and a few drops of the liquid
are ultimately tested with hydrogen sulphide or ammonia. The
remainder of zinc dust is then weighed, and its value deducted from the
original weight. Zinc and cadmium of the filtrate are determined as
above. On repeating this method several times most satisfactory results
are obtained.
Another mode of operating is to employ an excess of copper sulphate
and to determine the copper dissolved in the filtrate. The separation of
copper from cadmium being difficult and laborious, and the volumetric
estimation with potassium cyanide not practicable, it is not prudent to
apply this method.
When calcined zinciferous pyrites have to be examined, the estimation
of zinc is similar to that employed in the analysis of zinc ore. The
sample is exhausted with water, filtered, and, to eliminate calcium
sulphate and basic iron sulphate, evaporated to dryness. It is then
dissolved in a small quantity of alcohol and water, refiltered, and the
filtrate decomposed with ammonium carbonate. The original residue is
treated with a solution of ammonium carbonate, which dissolves
arsenious acid and basic zinc sulphate, filtered, and united with the
first filtrate. When iron and manganese are present, the filtrates are
treated with bromine. The united filtrates are boiled or examined
volumetrically with sodium sulphide.
* * * * *
PETROLEUM AS FUEL IN LOCOMOTIVE ENGINES.[2]
[Footnote 2: Abstract of paper read before the Institution of
Mechanical Engineers.]
By Mr. THOMAS URQUHART.
Comparing naphtha refuse and anthracite, the former has a theoretical
evaporative power of 16.2 lb. of water per lb. of fuel, and the latter of
12.2 lb., at a pressure of 8 atm. or 120 lb. per square inch; hence
petroleum has, weight for weight, 33 per cent. higher evaporative value
than anthracite. Now in locomotive practice a mean evaporation of
from 7 lb. to 7½ lb. of water per lb. of anthracite is about what is
generally obtained, thus giving about 60 per cent. efficiency, while 40
per cent. of the heating power is unavoidably lost. But with petroleum
an evaporation of 12.25 lb. is practically obtained, giving 12.25/16.2 =
75 per cent. efficiency. Thus in the first place petroleum is theoretically
33 per cent. superior to anthracite in evaporative power; and secondly,
its useful effect is 25 per cent. greater, being 75 percent. instead of 60
percent.; while, thirdly, weight for weight, the practical evaporative
value of petroleum must be reckoned as at least from (12.25 -
7.50)/7.50 = 63 per cent. to (12.25 - 7.00)/7.00 = 75 per cent. higher
than that of anthracite.
Spray injector.--Steam not superheated, being the most convenient for
injecting the spray of liquid fuel into the furnace, it remains to be
proved how far superheated steam or compressed air is really superior
to ordinary saturated steam, taken from the highest point inside the
boiler by a special internal pipe. In using several systems of spray
injectors for locomotives, the author invariably noticed the
impossibility of preventing leakage of tubes, accumulation of soot, and
inequality of heating of the fire box. The work of a locomotive boiler is
very different from that of a marine or stationary boiler, owing to the
frequent changes of gradient on the line, and the frequent stoppages at
stations. These conditions render firing with petroleum very difficult;
and were it not for the part played by properly arranged brickwork
inside the fire box, the spray jet alone would be quite inadequate.
Hitherto the efforts of engineers have been mainly directed toward
arriving at the best kind of "spray injector," for so minutely subdividing
a jet of petroleum into a fine spray, by the aid of steam or compressed
air, as to render it inflammable and of easy ignition. For this object
nearly all the known spray injectors have very long and narrow orifices
for petroleum as well as for steam; the width of the orifices does not
exceed from ½ mm. to 2 mm. or 0.02 in. to 0.08 in., and in many
instances
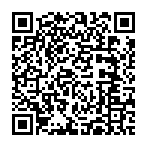
Continue reading on your phone by scaning this QR Code
Tip: The current page has been bookmarked automatically. If you wish to continue reading later, just open the
Dertz Homepage, and click on the 'continue reading' link at the bottom of the page.