of iron with the same paint; when the wood takes up part of the oil from the paint and leaves the rest in proportion to harden well, where at the same time the paint on iron remains soft. To be more lucid, it need be explained, linseed oil boiled has lost its oleic acid and glycerine ether, which form with the bases of pigments the insoluble soap, as well as its albumen, which in boiling is thrown out. It coagulates at 160�� F. heat; each is needed to better withstand the action of wind and weather, preventing the dust from attaching itself to a painted surface, a channel for ammonia in damp weather to dissolve and wash off the paint. In later years linseed oil has been extracted from linseed meal by the aid of naphtha and percolation, the product of a very clear, quick drying oil, but lacking in its binding quality, no doubt caused by the naphtha dissolving the fatty matter only, leaving the glycerine and albumen in the meal.
All pigments of paint group according to their affinity to raw linseed oil into three classes. First, those that form chemical combinations, called soap. This kind is the most durable, is used for priming purposes, and consists of lead, zinc, and iron bases, of which red lead takes up the most oil; next, white lead, the pure carbonate Dutch process made, following with zinc white and iron carbonates, as iron ore paint, Turkey umber, yellow ocher; also faintly the chromates of lead--chrome-green and chrome-yellow, finishing with the poorest of all, modern white lead, made by the wet or vinegar process. The second class being neutrals have no chemical affinity to linseed oil; they need a large quantity of drier to harden the paint, and include all blacks, vermilion, Prussian, Paris, and Chinese blue, also terra di Sienna, Vandyke brown, Paris green, verdigris, ultramarine, genuine carmine, and madderlake. The last seven are, on account of their transparency, better adapted for varnish mixtures--glazing. The third class of pigments act destructively to linseed oil; they having an acid base (mostly tin salt, hydrochloride of tin, and redwood dye), form with the gelatinous matter of the oil a jelly that will neither work well under the brush nor harden sufficiently, and can be used in varnish for glazing only; they are not permanent in color, and among the most troublesome are the lower grades of so-called carmines, madderlakes, rose pinks, etc., which contain more or less acidous dyes, forming a soft paint with linseed oil that once dry on a job can be twisted or peeled off like the skin of a ripe peach. All these combinations of paint have to be closely observed by the painter to insure his success.
Twenty-five years ago a house needed to be painted outside but once in from five to seven years; it looked well all the time, as no dust settled in the paint to make it unsightly. Painters then used the Dutch-process-made white-lead, a base and raw linseed oil, a fat acid, which formed the insoluble soap. They also put turpentine in the following coats, to keep up the proportions of oil and pigment. All held out well against wind and weather. Now they use the wet-process-made white lead, neutralized by vinegar, with oil neutralized by boiling, from the first to the last coat, and--fail in making their work permanent.
W.S., in the Building News, relates an unaccountable mysterious blistering in a leaky house, where the rainwater came from above on a painted wood wall, blistering the paint in streaks and filled at the lower ends with water, which no doubt was caused by the water soaking the wood at the upper ends where there was no paint, and following it down through the fibers, pushed and peeled off the soft, inadhesive paint. Green, sappy, and resinous wood is unfit for durable painting, and to avoid blistering and peeling wood should be well seasoned and primed with all raw linseed oil, some drier, to insure a moderately slow drying, and as much of a base pigment as the painter can possibly spread (much drier takes up too much oil acid, needed for the pigment base to combine with), which insures a tough paint that never fails to stand against blistering or peeling, as well as wind, weather, and ammonia.
The coach, car, and house painter can materially improve his painting where his needs lie by first oiling the wood with raw oil, then smoothing the surface down with lump pumicestone, washing it with a mixture of japan drier or, better yet, gold sizing and turpentine, wiping dry, and following it up with a coat of white lead, oil, and turpentine. The explanation is: the raw oil penetrates the wood and raises the wood fibers on the surface
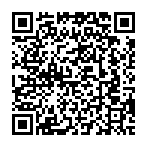
Continue reading on your phone by scaning this QR Code
Tip: The current page has been bookmarked automatically. If you wish to continue reading later, just open the
Dertz Homepage, and click on the 'continue reading' link at the bottom of the page.