which involved a cost of about ��4. The modern requirements of trade have in every branch of industry ruthlessly compelled the abandonment of the slow, easy-going methods which satisfied the times when competition was less keen. Automatic mechanical arrangements, almost at every turn, more effectually and at greatly increased speed, complete manufacturing operations previously performed by hand, and oil-seed crushing machinery has been no exception to the general rule. The illustrations we give represent the latest developments in improved oil-mill machinery introduced by Rose, Downs & Thompson, named the "Colonial" mill, and recently we had an opportunity of inspecting the machinery complete before shipment to Calcutta, where it is being sent for the approaching exhibition. As compared with the old system of oil-seed crushing, Messrs. Rose, Downs & Thompson claim for their method, among other advantages, a great saving in driving power, economy of space, a more perfect extraction of the oil, an improved branding of the cakes, a saving of 50 per cent. in the labor employed in the press-room, with also a great saving in wear and tear, while the process is equally applicable to linseed, cottonseed, rapeseed, or similar seeds. In addition to these improvements in the system, the "Colonial" mill has been specially designed in structural arrangement to meet the requirements of exporters. The machinery and engine are self-contained on an iron foundation, so that there is no need of skilled mechanics to erect the mill, nor of expensive stone foundations, while the building covering the mill can, if desired, be of the lightest possible description, as no wall support is required. The mill consists of the following machinery: A vertical steel boiler, 3 ft. 7 in. diameter, 8 ft. 1? in. high, with three cross tubes 7? in. diameter, shell 5/16 in. thick, crown 3/8 in. thick, uptake 9 in. diameter, with all necessary fittings, and where wood fuel is used extra grate area can be provided. This boiler supplies the steam not only for the engine, but also for heating and damping the seed in the kettle. The engine is vertical, with 8 in. cylinder and 12 in. stroke, with high speed governors, and stands on the cast iron bed-plate of the mill. This bed-plate, which is in three sections, is about 30 ft. long, and is planed and shaped to receive the various machines, which, when the top is leveled, can be fixed in their respective places by any intelligent man, and when the machines are in position they form a support for the shafting. The seed to be crushed is stored in a wooden bin, placed above and behind the roll frame hopper. The roll frame has four chilled cast iron rolls, 15 in. face, 12 in. diameter, so arranged as to subject the seed to three rollings, with patent pressure giving apparatus. These rolls are driven by fast and loose pulleys by the shaft above. After the last rolling the seed falls through an opening in the foundation plate in a screen driven from the bottom roll shaft by a belt. This conveys the seed in a trough to a set of elevators, which supply it continuously to the kettle. This kettle, which is 3 ft. 6 in. internal diameter and 20 in. deep, is made of cast iron and of specially strong construction. There is only one steam joint in it, and to reduce the liability of leakage this joint is faced in a lathe. The inside furnishings of the kettle are a damping apparatus with perforated boss, upright shaft, stirrer, and delivery plate, and patent slide. The kettle body is fitted with a wood frame and covered with felt, which is inclosed within iron sheeting. The crushed seed is heated in the kettle to the required temperature by steam from the boiler, and it is also damped by a jet of steam which is regulated by a wheel valve with indicating plate. When the required temperature has been obtained, the seed is withdrawn by a measuring box through a self-acting shuttle in the kettle bottom, and evenly distributed over a strip of bagging supported on a steel tray in a Virtue patent moulding machine, where it undergoes a compression sufficient to reduce it to the size that can be taken in by the presses, but not sufficient to cause any extraction of the oil. The seed leaves the moulding machine in the form of a thick cake from nine to eleven pounds in weight, and each press is constructed to take in twelve of these cakes at once. The press cylinders are 12 in. diameter and are of crucible cast steel. To insure strength of construction and even distribution of strain throughout the press, all the columns, cylinders, rams, and heads are planed and turned accurately to gauges, and
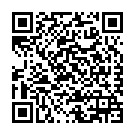
Continue reading on your phone by scaning this QR Code
Tip: The current page has been bookmarked automatically. If you wish to continue reading later, just open the
Dertz Homepage, and click on the 'continue reading' link at the bottom of the page.