referred to the next chapter, which deals with the manner of setting and
holding them to do the most effective work.
When it is understood that a cutting tool in a lathe is simply a form of
wedge which peels off a definite thickness of metal, the importance of
proper grinding and correct position in the lathe can be appreciated.
ROUGHING TOOLS.--The most useful is the roughing tool to take off
the first cut. As this type of tool is also important, with some
modifications, in finishing work, it is given the place of first
consideration here.
[Illustration: Fig. 24. Tool for Wrought iron. Fig. 25. Tool for Cast
iron.]
Fig. 24 shows side and top views of a tool designed to rough off
wrought iron, or a tough quality of steel. You will notice, that what is
called the top rake (A) is very pronounced, and, as the point projects
considerably above the body of the tool itself, it should, in practice, be
set with its cutting point above the center.
THE CLEARANCE.--Now, in grinding, the important point is the
clearance line (B). As shown in this figure, it has an angle of 10
degrees, so that in placing the tool in the holder it is obvious it cannot
be placed very high above the center, particularly when used on small
work. The top rake is ground at an angle of 60 degrees from the vertical.
The arc of the curved end depends on the kind of lathe and the size of
the work.
The tool (Fig. 25), with a straight cutting edge, is the proper one to
rough off cast iron. Note that the top rake (C) is 70 degrees, and the
clearance 15 degrees.
THE CUTTING ANGLE.--Wrought iron, or mild steel, will form a
ribbon when the tool wedges its way into the material. Cast iron, on the
other hand, owing to its brittleness, will break off into small particles,
hence the wedge surface can be put at a more obtuse angle to the work.
In grinding side-cutters the clearance should be at a less angle than 10
degrees, rather than more, and the top rake should also be less;
otherwise the tendency will be to draw the tool into the work and swing
the tool post around.
DRILLS.--Holders for grinding twist drills are now furnished at very
low prices, and instructions are usually sent with the machines, but a
few words may not be amiss for the benefit of those who have not the
means to purchase such a machine.
Hand grinding is a difficult thing, for the reason that through
carelessness, or inability, both sides of the drill are not ground at the
same angle and pitch. As a result the cutting edge of one side will do
more work than the other. If the heel angles differ, one side will draw
into the work, and the other resist.
[Illustration: Fig. 26. End view. Fig. 27. Side view.]
WRONG GRINDING.--When such is the case the hole becomes untrue.
The sides of the bit will grind into the walls, or the bit will have a
tendency to run to one side, and particularly if boring through metal
which is uneven in its texture or grain.
Figs. 26 and 27 show end and side views of a bit properly ground. If a
bit has been broken off, first grind it off square at the end, and then
grind down the angles, so that A is about 15 degrees, and be sure that
the heel has sufficient clearance--that is, ground down deeper than the
cutting point.
CHISELS.--A machine shop should always have a plentiful supply of
cold chisels, and a particular kind for each work, to be used for that
purpose only. This may seem trivial to the boy, but it is really a most
important matter.
Notice the careless and incompetent workman. If chipping or cutting is
required, he will grasp the first chisel at hand. It may have a curved end,
or be a key-way chisel, or entirely unsuited as to size for the cutting
required.
The result is an injured tool, and unsatisfactory results. The rule holds
good in this respect as with every other tool in the kit. Use a tool for
the purpose it was made for, and for no other. Acquire that habit.
COLD CHISELS.--A cold chisel should never be ground to a long,
tapering point, like a wood chisel. The proper taper for a wood chisel is
15 degrees, whereas a cold chisel should be 45 degrees. A drifting
chisel may have a longer taper than one used for chipping.
It is a good habit, particularly as there are so few tools which require
grinding, to commence the day's work by grinding the chisels, and
arranging them for business.
SYSTEM IN WORK.--Then see to
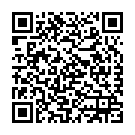
Continue reading on your phone by scaning this QR Code
Tip: The current page has been bookmarked automatically. If you wish to continue reading later, just open the
Dertz Homepage, and click on the 'continue reading' link at the bottom of the page.