too hot at that point; if the fracture can be cut with a file, the
metal was not hot enough at that point.
When hardening carbon tool steel its heat should be brought to a cherry
red, the exact degree of heat depending on the amount of carbon and
the test made, then plunged into water and held there until all hissing
sound and vibration ceases. Brine may be used for this purpose; it is
even better than plain water. As soon as the hissing stops, remove the
work from the water or brine and plunge in oil for complete cooling.
[Illustration: Figure 6.--Cooling the Tool for Tempering]
In hardening high-speed tool steel, or air hardening steels, the tool
should be handled as for carbon steel, except that after the body reaches
a cherry red, the cutting point must be quickly brought to a white heat,
almost melting, so that it seems ready for welding. Then cool in an oil
bath or in a current of cool air.
Hardening of copper, brass and bronze is accomplished by hammering
or working them while cold.
Tempering is the process of making steel tough after it has been
hardened, so that it will hold a cutting edge and resist cracking.
Tempering makes the grain finer and the metal stronger. It does not
affect the hardness, but increases the elastic limit and reduces the
brittleness of the steel. In that tempering is usually performed
immediately after hardening, it might be considered as a continuation
of the former process.
The work or tool to be tempered is slowly heated to a cherry red and
the cutting end is then dipped into water to a depth of 1/2 to 3/4 inch
above the point (Figure 6). As soon as the point cools, still leaving the
tool red above the part in water, remove the work from the bath and
quickly rub the end with a fine emery cloth.
As the heat from the uncooled part gradually heats the point again, the
color of the polished portion changes rapidly. When a certain color is
reached, the tool should be completely immersed in the water until
cold.
For lathe, planer, shaper and slotter tools, this color should be a light
straw.
Reamers and taps should be cooled from an ordinary straw color.
Drills, punches and wood working tools should have a brown color.
Blue or light purple is right for cold chisels and screwdrivers.
Dark blue should be reached for springs and wood saws.
Darker colors than this, ranging through green and gray, denote that the
piece has reached its ordinary temper, that is, it is partially annealed.
After properly hardening a spring by dipping in lard or fish oil, it
should be held over a fire while still wet with the oil. The oil takes fire
and burns off, properly tempering the spring.
Remember that self-hardening steels must never be dipped in water,
and always remember for all work requiring degrees of heat, that the
more carbon, the less heat.
_Case Hardening._--This is a process for adding more carbon to the
surface of a piece of steel, so that it will have good wear-resisting
qualities, while being tough and strong on the inside. It has the effect of
forming a very hard and durable skin on the surface of soft steel,
leaving the inside unaffected.
The simplest way, although not the most efficient, is to heat the piece
to be case hardened to a red heat and then sprinkle or rub the part of the
surface to be hardened with potassium ferrocyanide. This material is a
deadly poison and should be handled with care. Allow the cyanide to
fuse on the surface of the metal and then plunge into water, brine or
mercury. Repeating the process makes the surface harder and the hard
skin deeper each time.
Another method consists of placing the piece to be hardened in a bed of
powdered bone (bone which has been burned and then powdered) and
cover with more powdered bone, holding the whole in an iron tray.
Now heat the tray and bone with the work in an oven to a bright red
heat for 30 minutes to an hour and then plunge the work into water or
brine.
CHAPTER II
OXY-ACETYLENE WELDING AND CUTTING MATERIALS
_Welding._--Oxy-acetylene welding is an autogenous welding process,
in which two parts of the same or different metals are joined by causing
the edges to melt and unite while molten without the aid of hammering
or compression. When cool, the parts form one piece of metal.
The oxy-acetylene flame is made by mixing oxygen and acetylene
gases in a special welding torch or blowpipe, producing, when burned,
a heat of 6,300 degrees, which is more than twice the melting
temperature of the common metals. This flame, while
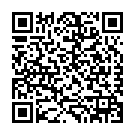
Continue reading on your phone by scaning this QR Code
Tip: The current page has been bookmarked automatically. If you wish to continue reading later, just open the
Dertz Homepage, and click on the 'continue reading' link at the bottom of the page.