and lead.
White metal is one form of bearing bronze containing over 80 per cent
of zinc together with copper, tin, antimony and lead. Another form is
made with nearly 90 per cent of tin combined with copper and
antimony.
Gun metal bronze is made from 90 per cent copper with 10 per cent of
tin and is used for heavy bearings, brackets and highly finished parts.
Phosphor bronze is used for very strong castings and bearings. It is
similar to gun metal bronze, except that about 1-1/2 per cent of
phosphorus has been added.
Manganese bronze contains about 1 per cent of manganese and is used
for parts requiring great strength while being free from corrosion.
German silver is made from 60 per cent of copper with 20 per cent each
of zinc and nickel. Its high electrical resistance makes it valuable for
regulating devices and rheostats.
Tin is the principal part of babbitt and solder. A commonly used
babbitt is composed of 89 per cent tin, 8 per cent antimony and 3 per
cent of copper. A grade suitable for repairing is made from 80 per cent
of lead and 20 per cent antimony. This last formula should not be used
for particular work or heavy loads, being more suitable for spacers.
Innumerable proportions of metals are marketed under the name of
babbitt.
Solder is made from 50 per cent tin and 50 per cent lead, this grade
being called "half-and-half." Hard solder is made from two-thirds tin
and one-third lead.
Aluminum forms many different alloys, giving increased strength to
whatever metal it unites with.
Aluminum brass is composed of approximately 65 per cent copper, 30
per cent zinc and 5 per cent aluminum. It forms a metal with high
tensile strength while being ductile and malleable.
Aluminum zinc is suitable for castings which must be stiff and hard.
Nickel aluminum has a tensile strength of 40,000 pounds per square
inch.
Magnalium is a silver-white alloy of aluminum with from 5 to 20 per
cent of magnesium, forming a metal even lighter than aluminum and
strong enough to be used in making high-speed gasoline engines.
HEAT TREATMENT OF STEEL
The processes of heat treatment are designed to suit the steel for
various purposes by changing the size of the grain in the metal,
therefore the strength; and by altering the chemical composition of the
alloys in the metal to give it different physical properties. Heat
treatment, as applied in ordinary shop work, includes the three
processes of annealing, hardening and tempering, each designed to
accomplish a certain definite result.
All of these processes require that the metal treated be gradually
brought to a certain predetermined degree of heat which shall be
uniform throughout the piece being handled and, from this point,
cooled according to certain rules, the selection of which forms the
difference in the three methods.
_Annealing._--This is the process which relieves all internal strains and
distortion in the metal and softens it so that it may more easily be cut,
machined or bent to the required form. In some cases annealing is used
only to relieve the strains, this being the case after forging or welding
operations have been performed. In other cases it is only desired to
soften the metal sufficiently that it may be handled easily. In some
cases both of these things must be accomplished, as after a piece has
been forged and must be machined. No matter what the object, the
procedure is the same.
The steel to be annealed must first be heated to a dull red. This heating
should be done slowly so that all parts of the piece have time to reach
the same temperature at very nearly the same time. The piece may be
heated in the forge, but a much better way is to heat in an oven or
furnace of some type where the work is protected against air currents,
either hot or cold, and is also protected against the direct action of the
fire.
[Illustration: Figure 4.--A Gaspipe Annealing Oven]
Probably the simplest of all ovens for small tools is made by placing a
piece of ordinary gas pipe in the fire (Figure 4), and heating until the
inside of the pipe is bright red. Parts placed in this pipe, after one end
has been closed, may be brought to the desired heat without danger of
cooling draughts or chemical change from the action of the fire. More
elaborate ovens may be bought which use gas, fuel oils or coal to
produce the heat and in which the work may be placed on trays so that
the fire will not strike directly on the steel being treated.
If the work is not very important, it may be withdrawn from the fire or
oven, after heating to the
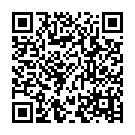
Continue reading on your phone by scaning this QR Code
Tip: The current page has been bookmarked automatically. If you wish to continue reading later, just open the
Dertz Homepage, and click on the 'continue reading' link at the bottom of the page.