and the metal is found to be hard and brittle. When the iron is slowly cooled and then broken the fracture is gray and the iron is more malleable and less brittle. If cast iron contains sulphur or phosphorus, it will show a white fracture regardless of the rapidity of cooling, being brittle and less desirable for general work.
_Steel._--Steel is composed of extremely minute particles of iron and carbon, forming a network of layers and bands. This carbon is a smaller proportion of the metal than found in cast iron, the percentage being from 3/10 to 2-1/2 per cent.
Carbon steel is specified according to the number of "points" of carbon, a point being one one-hundredth of one per cent of the weight of the steel. Steel may contain anywhere from 30 to 250 points, which is equivalent to saying, anywhere from 3/10 to 2-1/2 per cent, as above. A 70-point steel would contain 70/100 of one per cent or 7/10 of one per cent of carbon by weight. The percentage of carbon determines the hardness of the steel, also many other qualities, and its suitability for various kinds of work. The more carbon contained in the steel, the harder the metal will be, and, of course, its brittleness increases with the hardness. The smaller the grains or particles of iron which are separated by the carbon, the stronger the steel will be, and the control of the size of these particles is the object of the science of heat treatment.
In addition to the carbon, steel may contain the following:
Silicon, which increases the hardness, brittleness, strength and difficulty of working if from 2 to 3 per cent is present.
Phosphorus, which hardens and weakens the metal but makes it easier to cast. Three-tenths per cent of phosphorus serves as a hardening agent and may be present in good steel if the percentage of carbon is low. More than this weakens the metal.
Sulphur, which tends to make the metal hard and filled with small holes.
Manganese, which makes the steel so hard and tough that it can with difficulty be cut with steel tools. Its hardness is not lessened by annealing, and it has great tensile strength.
Alloy steel has a varying but small percentage of other elements mixed with it to give certain desired qualities. Silicon steel and manganese steel are sometimes classed as alloy steels. This subject is taken up in the latter part of this chapter under _Alloys_, where the various combinations and their characteristics are given consideration.
Steel has a tensile strength varying from 50,000 to 300,000 pounds per square inch, depending on the carbon percentage and the other alloys present, as well as upon the texture of the grain. Steel is heavier than cast iron and weighs about the same as wrought iron. It is about one-ninth as good a conductor of electricity as copper.
Steel is made from cast iron by three principal processes: the crucible, Bessemer and open hearth.
Crucible steel is made by placing pieces of iron in a clay or graphite crucible, mixed with charcoal and a small amount of any desired alloy. The crucible is then heated with coal, oil or gas fires until the iron melts, and, by absorbing the desired elements and giving up or changing its percentage of carbon, becomes steel. The molten steel is then poured from the crucible into moulds or bars for use. Crucible steel may also be made by placing crude steel in the crucibles in place of the iron. This last method gives the finest grade of metal and the crucible process in general gives the best grades of steel for mechanical use.
[Illustration: Figure 2.--A Bessemer Converter]
Bessemer steel is made by heating iron until all the undesirable elements are burned out by air blasts which furnish the necessary oxygen. The iron is placed in a large retort called a converter, being poured, while at a melting heat, directly from the blast furnace into the converter. While the iron in the converter is molten, blasts of air are forced through the liquid, making it still hotter and burning out the impurities together with the carbon and manganese. These two elements are then restored to the iron by adding spiegeleisen (an alloy of iron, carbon and manganese). A converter holds from 5 to 25 tons of metal and requires about 20 minutes to finish a charge. This makes the cheapest steel.
[Illustration: Figure 3.--An Open Hearth Furnace]
Open hearth steel is made by placing the molten iron in a receptacle while currents of air pass over it, this air having itself been highly heated by just passing over white hot brick (Figure. 3). Open hearth steel is considered more uniform and reliable than Bessemer, and is used for springs, bar steel, tool steel, steel plates, etc.
Aluminum is one of the commonest industrial metals. It
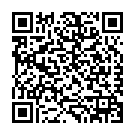
Continue reading on your phone by scaning this QR Code
Tip: The current page has been bookmarked automatically. If you wish to continue reading later, just open the
Dertz Homepage, and click on the 'continue reading' link at the bottom of the page.