and leave it to cool. If the fire is kindled at sunset, the charcoal is ready for use next morning.
The smith makes his own blow-pipe, out of brass, usually by beating a piece of thick brass wire into a flat strip, and then bending this into a tube. The pipe is about a foot long, slightly tapering and curved at one end; there is no arrangement for retaining the moisture proceeding from the mouth. These Indians do not understand our method of making an air chamber of the mouth; they blow with undistended cheeks, hence the current of air directed on the flame is intermitting. The flame used in soldering with the blow-pipe is derived from a thick braid of cotton rags soaked in mutton suet or other grease. Their borax is purchased from the whites, and from the same source is derived the fine wire with which they bind together the parts to be soldered. I have been told by reliable persons that it is not many years since the Navajos employed a flux mined by themselves in their own country; but, finding the pure borax introduced by the traders to be much better, they gradually abandoned the use of the former substance.
For polishing, they have sand-paper and emery-paper purchased from the whites; but as these are expensive, they are usually required only for the finishing touches, the first part of the work being done with powdered sandstone, sand, or ashes, all of which are used with or without water. At certain stages in the progress of the work, some articles are rubbed on a piece of sandstone to reduce the surfaces to smoothness; but the stone, in this instance, is more a substitute for the file than for the sand-paper. Perhaps I should say that the file is a substitute for the stone, for there is little doubt that stone, sand, and ashes preceded file and paper in the shop of the Indian smith.
For blanching the silver, when the forging is done, they use a mineral substance found in various parts of their country, which, I am informed by Mr. Taylor, of the Smithsonian Institution, is a "hydrous sulphate of alumina," called almogen. This they dissolve in water, in a metal basin, with the addition, sometimes, of salt. The silver, being first slightly heated in the forge, is boiled in this solution and in a short time becomes very white.
The processes of the Navajo silversmith may be best understood from descriptions of the ways in which he makes some of his silver ornament. I once engaged two of the best workmen in the tribe to come to Fort Wingate and work under my observation for a week. They put up their forge in a small outbuilding at night, and early next morning they were at work. Their labor was almost all performed while they were sitting or crouching on the ground in very constrained positions; yet I never saw men who worked harder or more steadily. They often labored from twelve to fifteen hours a day, eating their meals with dispatch and returning to their toil the moment they had done. Occasionally they stopped to roll a cigarette or consult about their work, but they lost very few moments in this way. They worked by the job and their prices were such that they earned about two dollars a day each.
The first thing they made was a powder charger with a handle in the shape of a dart (Fig. 2, Pl. XIX). Having cut in sandstone rock (Fig. 2, Pl. XVIII) the necessary grooves for molds and greased the same, they melted two Mexican dollars--one for the bowl or receptacle, and one for the handle--and poured each one into its appropriate mold. Then each smith went to work on a separate part; but they helped one another when necessary. The ingot cast for the receptacle was beaten into a plate (triangular in shape, with obtuse corners), of a size which the smith guessed would be large enough for his purpose. Before the process of bending was quite completed the margins that were to form the seam were straightened by clipping and filing so as to assume a pretty accurate contact, and when the bending was done, a small gap still left in the seam was filled with a shred of silver beaten in. The cone, at this stage, being indented and irregular, the workman thrust into it a conical stake or mandrel, which he had formed carefully out of hard wood, and with gentle taps of the hammer soon made the cone even and shapely. Next, withdrawing the stake, he laid on the seam a mixture of borax and minute clippings of silver moistened with saliva, put the article into the fire, seam up, blew with the bellows
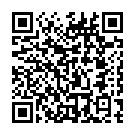
Continue reading on your phone by scaning this QR Code
Tip: The current page has been bookmarked automatically. If you wish to continue reading later, just open the
Dertz Homepage, and click on the 'continue reading' link at the bottom of the page.