in response to requests. The checklist may be useful in Regional Occupational Programs (ROP) and supervisory and crew chief training.
Correcting a mistake starts with understanding what went wrong.
One rarely reads a newspaper without noting a report about a foodstuff, medication, or device on the market or in use for its intended purpose, was recalled by the manufacturer. Whatever it is, it was not doing the task for which it was intended or designed, and continued use might risk life, quality of life, or property.
For example, a national business newspaper reported that a motor vehicle manufacturer was recalling more that 100,000 vehicles of various models. The reason was faulty secondary door latches, and an electrical harness support device in which an electrical short might occur, possibly causing a fire.
Faulty manufacture, construction, inspection or training in any function concerned with manufacturing a product or providing a service all too often have serious consequences.
What follows is based on my Inspector General experiences in tracking compliance with 'corrective action' commitments for mistakes and deficiencies at a major military industrial facility. The errors had been noted and reported on by higher headquarters and private sector technical and management inspection teams.??
Management and technical inspection and other oversight methods have changed significantly with computerization. Nevertheless, mistakes still happen, at times the same as before computerization, and they continue to happen. Management oversight and controls over fixing mistakes and their causes need to keep abreast with the analyses of a mistake's occurrence, its complexity and safety implications, and other immediate and ripple effects of the event. Useful ideas on preventing and fixing mistakes need to cross feed across all elements and levels of our society. Ignoring cross feed escalates the unconscionable waste of the nation's and the world's resources and could increase needless loss of lives and property.??
In my work as an Inspector General's analyst at a major Air Force logistics base I prepared a checklist of elements to be considered in planning corrective actions for mistakes in various supply and maintenance shops. I discussed and distributed the checklist during seminars that I conducted on the subject for crew chiefs and first and second line supervisors. My hope was that the check list would also be useful to managers, line-and-staff supervisors, procedures specialists, product-line workers and crew chiefs, and teachers and students at vocational and other schools of public and private sector enterprises and institutions. The checklist was subsequently published by the Small Business Administration as Management Aid MA242 Fixing Production Mistakes and widely distributed to industry, libraries and vocational schools.??
#
The checklist suggests a few of the many steps and considerations that go into preparing for and following through on a 'fix' for a mistake in manufacturing, support, services, or other operations in the work place. Record keeping has improved with the computer; but it's still up to people to think the problem through, arrive at resolutions, and ensure that the fix is implemented and effective.
The options are shown in checklist form and any one of them may or may not apply to a specific situation in a shop or office. The fact is that any one mistake, and its causes and effects, as a collection of distinct but interacting events, is unique and needs to be addressed in that context. There is no general all-purpose after-the-fact corrective action plan, nevertheless, generalized contingency planning, for example, in the form of a documented Practice on getting organized around the corrective action job would be useful. The objective is to (1) fix the mistake, (2) keep it from happening again, and (3) integrate what was learned from the experience into the organization's existing engineering and other production functions, training and other management systems.
Although the mistake (event) and the fix relates to a manufactured product, the options (check list elements) might be applicable or adaptable to public and private sector construction, health care, support and services, general administration, and other functions and processes, as appropriate to the reader's interests.
The coverage given here is intentionally general; no two manufacturers, institutions, service entities, down to their first line work sites are exactly alike in their tasks, equipment layout, skills, environment, human factors, staff and supervisory personalities, etc. The interaction of all of these factors, within and outside the work unit, affects how an approved fix is installed and how it works out. The planning for and integration of a fix (the clarity of procedures and sequencing of who does what and when) takes into account the uniqueness of the problem and the work site or station.
#
Mistakes challenge a leader's sense of order. Timely and effective corrective action may be vital to the safety of a product, the welfare of consumers, and the stability of the organization in which the mistake occurred.
Each product, its design/production system and support functions have unique characteristics. Fixing a
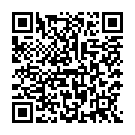
Continue reading on your phone by scaning this QR Code
Tip: The current page has been bookmarked automatically. If you wish to continue reading later, just open the
Dertz Homepage, and click on the 'continue reading' link at the bottom of the page.