in the transport/warehousing system, consumers, vendors
of components, and you, the manufacturer.
- Review relevant policies and procedures; activate the plant's
corrective actions task group; designate and appoint a task group leader;
prepare a comprehensive corrective action plan; select subordinate
(function) leaders, production staff and line crew chiefs, technicians,
and line workers; design and procure or manufacture replacement parts;
marshal tools, equipment and other resources; designate and commit
work stations, and implement the approved 'corrective action plan.'
- Notify and make/secure commitments to/from concerned entities that
are located outside of the plant. Integrate the fix and what was learned
from the experience, into the organization's management, engineering
(RDT&E), procurement, production and supporting management
systems to preclude the mistake's recurrence.
- Have you considered the demands that will be made on and the
adequacy and availability of your:Â
- Plant facilities (structural and environmental)?Â
- Finances/accounting? Â - Energy sources?Â
- Communications systems?Â
- Transportation?Â
- Public relations and marketing? Â - Shop equipment and tools
available and tested?Â
- Supplies and long-lead acquisition time materials?Â
- Data? Â - People (skills, training, safety, working hours, etc.)?
- Resources in other functions that will be involved?Â
- Can the faulty assemblies be processed economically for tear down to
get at and remove the defective part and then to return the remaining
(good) parts to your routine production system without disrupting the
product line?Â
- If not, do you need a special, one-time production task group for the
defective sub-assemblies to do the tear down, repair, and re-assembly
job?Â
- If, after teardown, the parts (minus the defective item) can be returned
to routine production, have you identified the points along the
production system where each good assembly and/or component can be
re-checked and reused?
- Have you identified all the work units and workstations that will be
directly affected by the rework of the faulty items?Â
- Do you know precisely how each will be affected?Â
- Do the supervisors and direct workers of those work units and at each
workstation understand the problem and what is expected of them? Â -
Have you ascertained which work units and workstations can be
by-passed during the fix to minimize disruption to routine operations
and production and thereby reduce cumulative adverse effects?Â
- Will the fix make it necessary to?Â
- Realign workspace?Â
- Move shop equipment?Â
- Modify tools and equipment?Â
- Fabricate jigs and special holding devices?Â
- Redesign parts and assemblies?Â
- Revise quality assurance standards and procedures, and production
practices? - Retrain people?Â
- Reschedule and reprogram other work?Â
- Modify contracts with suppliers and customers?Â
- Does fixing the mistake call for a documented Corrective Action Plan,
commitment of significant resources, and detailed production
scheduling?Â
- Can the corrective action taken as a result of this error be applied to
future designs, and management policies and practices, and for
production system improvements elsewhere in your plant?Â
- Has this experience given you ideas to improve your operations?Â
- Have you documented what you learned, tested them, and injected the
results into your plant practices?Â
#
A corrective action plan is forward-looking: it specifies the action steps
and their sequence for fixing the defective items and the changes that
need to be integrated into the product line management system. It is
positive-oriented and concentrates on the fix to the exclusion of looking
back for who did what and why. The investigative and blame job is not
planning and belongs to another group.Â
As a manager, supervisor and leader, take that extra step that prevents
the same or comparable mistakes from happening. What really caused
the problem? What can and should be done about it? Is a significant
change needed in tools, equipment, or materials? Should the shop
layout be changed? Do workers need additional training? Are product
inspection and quality assurance skills, methodologies and standards
tight enough? Are you using the right vendors? The mistake and its
underlying causes that were resolved at one shop location could
provide opportunities for a significant technical or management
improvement throughout the plant. Have you and your staff thought
through the possibility of recurrence, and have you done something
constructive to preclude its happening?
MEMOIR: THE FIRST LINE SUPERVISOR INSPECTS THE
WORK UNIT
I drafted this procedure in the 1960s when I was a management analyst
on the staff of an Inspector General at an Air Force logistics depot in
California. The concept, and its implementation, was presented at
seminars attended by the activity's crew chiefs and supervisors.
The concept and process lends itself to computerization in sequencing
steps in
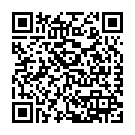
Continue reading on your phone by scaning this QR Code
Tip: The current page has been bookmarked automatically. If you wish to continue reading later, just open the
Dertz Homepage, and click on the 'continue reading' link at the bottom of the page.