the stocks from the cooks
were used, since a stock and its cooking condition can be judged
adequately only after it has been put through the various processes and
into the finished sheet of paper.
The first test consisted in making four separate cooks, Nos. 293, 294,
295, and 296, of approximately 300 pounds each, dividing the total
stock into two parts and making two separate paper tests. The first test
was made primarily in order to learn some of the qualities and
characteristics of the stock and to get the machinery equipment
adjusted properly. The yield of fiber was not determined in this
preliminary test, since the knowledge of it was not essential at this
stage of the work. The cooked stock which was emptied into the drainer
to be washed free from black liquor was composed largely of whole
pieces of hurds, but only slight pressure between the fingers was
required to crush the pieces. In the case of wood, this condition
ordinarily would indicate undercooking, but might not in the case of
hurds. Further observation on the action of the cooked stock during
subsequent processes was necessary in order to judge of its quality or
the suitability of the cooking conditions. The total cooked stock, about
500 pounds, was divided into two portions of 200 and 300 pounds,
respectively, and work was continued on them separately. The
200-pound test, designated as run No. 135, was put into a 350-pound
washing engine, washed one hour, and given a total light brush of 2-1/4
hours. The washing removed a great amount of dirt, but the engine did
not reduce the hurd stock as much as was desired. After heating the
stock in the beater to 40° C., it was bleached with bleaching-powder
solution, 94 gallons at 0.418 pound bleach per gallon, equivalent to
19.7 per cent of the fiber. This percentage of bleach is regarded as too
high for stock intended for book-paper manufacture, and subsequent
cooks therefore were given harder treatment in order to reduce this
figure. After draining and washing free from bleach residues, the stock
was furnished in the beater with 13 per cent of clay, 1 per cent of resin
size, and 2.5 per cent of alum, was tinted blue, given one hour's light
brush, and pumped to the stock chest. When running it on the paper
machine, the Jordan refiner seemed to have little effect in reducing
shives of undertreated wood, which indicated further the necessity of
harder cooking. The furnish acted well on the paper machine at 70 feet
per minute, but appeared somewhat too "free" on the wire. The paper
produced from this test is of very low quality, due to the improper
preparation of the stock, lack of sufficient bleach, the use of too small
an amount of blue tinting, and the presence of an excessive amount of
dirt, sand, and shives. The excessive amount of dirt and sand suggested
the sieving of the hurds before cooking, and this was performed in all
subsequent cooks.
The finish of the sheet is very poor, due to the fact that the calender
stack was composed of very light rolls which did not have a
satisfactory surface, yet the stack is known to be able to produce better
finishes if the proper stock is employed.
Run No. 136 was made on the 300-pound portion of stock from cooks
Nos. 293, 294, 295, and 296, and in essentially the same manner as run
No. 135. The stock was washed one hour, but given a brush of three
hours, and this brush was harder than in run No. 135. Bleach to the
extent of 19.8 per cent of the fiber was used, assisted by 1 pint of oil of
vitriol, and the resulting color was an improvement over that of run No.
135. After adding 13.5 per cent of clay and sizing with 1.1 per cent of
resin size, the furnish was given one-half hour's light brush, tinted, and
run on the machine, which was set at 70 feet per minute. This stock
acted better on the wire and gave no trouble on the machine, but it still
seemed to be impossible to reduce the wood shives by manipulation of
the Jordan refiner. The resulting sheet is an improvement over that
produced by No. 135, but is far from satisfactory.
Run No. 138 was made from hurds which, as in all subsequent tests,
were sieved on a 11-1/2-mesh wire screen until practically all the loose
dirt and sand was removed, which operation caused a loss averaging 3
per cent of the hurds. Stock from cooks Nos. 302 and 303 was used for
this run and the increased amount of caustic soda and the increase in
the time of cooking gave a stock of better appearance than those of
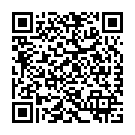
Continue reading on your phone by scaning this QR Code
Tip: The current page has been bookmarked automatically. If you wish to continue reading later, just open the
Dertz Homepage, and click on the 'continue reading' link at the bottom of the page.