fiber was used, the commercial product in the dry state was charged into the beating engine and disintegrated, after which the hurd stock was added in the wet condition.
Beating.--Beating is that operation concerning which the paper makers often say "there is where the paper is really made," and although the statement may not be literally true it contains a great deal of truth. It is the operation whereby the fibers are separated from each other, reduced to the proper lengths, and put in such a physical or chemical condition that they felt properly and form into a satisfactory sheet. It is probable that the quality of the sheet depends more upon the proper beater action than upon any other single operation. The action consists in drawing a water suspension of the fiber between two sets of rather blunt knives, one set being located in the bottom of a circulating trough and the other set on the periphery of a roll revolving just above the former set of knives. It is during this operation that the loading and sizing agents are incorporated and the whole furnish is tinted either to produce a satisfactory white or the desired color.
The term "paper making," as used in this publication, means the operation of forming the finished sheet of paper from stock which has been furnished and prepared in the beater. In these tests a 30-inch Fourdrinier machine of regular construction was used, a machine which often is used for the production of paper for filling regular commercial orders. The machine is designed to cause the water suspension of fibers to flow on to a traveling wire cloth, whereby the water drains away. More water is removed by passing the wet sheet through a series of press rolls, after which the sheet is dried on steam-heated drums and passed through polished iron rolls, which impart a finish to the sheet. A Jordan refining machine was employed in conjunction with the machine to improve further the quality of the fiber, and a pulp screen was used in order to remove coarse and extraneous materials from the fiber.
=DESCRIPTION OF TESTS.=
The nature of each complete paper test and the dependence of each operation on the others were such that it does not seem advisable to submit the results of the seven tests in tabular form. The numerous cooks, however, which furnished the pulp for the paper tests are presented in Table I in all essential detail.
TABLE I.--Data on cooking hemp hurds.
------+-----------+------------+----------+--------------------+----------- | | | | | | | | | Cooking | Yield of | Caustic |Strength of | | | bone-dry | soda used |caustic soda|Causticity+--------+-----------+ fiber Cook |(percentage| (grams per | of soda | | |(percentage No. |of bone-dry| liter). | solution.| Time |Temperature|of bone-dry | hurds). | | |(hours).| (°C.) | unsieved | | | | | | hurds). ------+-----------+------------+----------+--------+-----------+----------- 293 | 20.6| 100 | 75.3| 3| 166| 294 | 21 | 100 | 75.3| 3| 166| 295 | 21.6| 100 | 75.3| 3| 166| 296 | 20.3| 100 | 75.3| 3| 166| 301 | 21.9| 100 | 82.5| 4| 166| [3] 302 | 24.4| 100 | 82.5| 4| 166| 303 | 24.2| 100 | 84.3| 4| 166| 44.1 304 | 25 | 100 | 84.3| 4| 170| 39.5 305 | 25 | 100 | 84.3| 5| 170| 39.4 306 | 27.8| 107.5| 84.3| 4| 166| 36.5 307 | 26.7| 107 | 84.4| 5| 170| 38.1 308 | 26 | 107 | 84.4| 5| 170|\_ 37.3 309 | 27.3| 107 | 84.4| 5| 170|/ 310 | 27.1| 107 | 84.4| 6| 170| 37.0 311 | 27.2| 107 | 84.4| 6| 170| 36.8 312 | 28.3| 116.5| 85.5| 5| 170| 35.9 313 | 29.1| 113.1| 84.9| 5| 170|\_ 35.2 314 | 29.1| 109 | 83.9| 5| 170|/ 315 | 29.4| 109 | 83.9| 5| 170| 34.9 316 | 30 | 109.5| 84.9| 5| 170| 37.2 317 | 29.6| 109.5| 84.9| 5| 170| 37.0 318 | 29.6| 107 | 84.8| 5| 170| 37.7 319 | 29.4| 107.5| 84.2| 5| 170|\_ 35.4 320 | 29.3| 107.5| 84.2| 5| 170|/ ------+-----------+------------+----------+--------+-----------+-----------
[Footnote 3: Stock not used; dirty.]
Discussion of the various cooks will be given in connection with the descriptions of those paper tests in which the stocks from the cooks were used, since a stock and its cooking condition can be judged adequately only after it has been put through the various processes and into the finished sheet of paper.
The first test consisted in making four separate cooks, Nos. 293, 294, 295, and 296, of approximately 300 pounds each, dividing the total stock into two parts and making two separate paper tests. The first test was made primarily in order to learn some of the qualities and characteristics of the stock and to get the machinery equipment adjusted properly. The
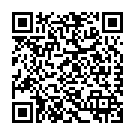
Continue reading on your phone by scaning this QR Code
Tip: The current page has been bookmarked automatically. If you wish to continue reading later, just open the
Dertz Homepage, and click on the 'continue reading' link at the bottom of the page.