give
way to the whiter resins; but where hardness and tenacity are essential
it must be adhered to, and where both are necessary a mixed varnish
must be used. This mixed varnish should be made from the picked
seed-lac as directed in the case of the white japan grounds. The
common seed-lac varnish may be made thus: Take 1-1/2 lb. of seed-lac
and wash it well in several waters, then dry it and powder it coarsely
and put it with a gallon of methylated spirits into a Bohemian glass
flask so that it be not more than two-thirds full. Shake the mixture well
together and place the flask in a gentle heat till the seed-lac appears to
be dissolved, the shaking being in the meantime repeated as often as
may be convenient; then pour off all the clear and strain the remainder
through a coarse cloth. The varnish so prepared must be kept for use in
a well-corked glass vessel. The whiter seed-lac varnishes are used in
the same manner as the common, except as regards the substances used
in polishing, which, where a pure white or the greater clearness or
purity of other pigments is in question, should be itself white, while the
browner sorts of polishing dust, as being cheaper and doing their
business with greater dispatch, may be used in other cases. The pieces
of work to be varnished should be placed near the fire or in a warm
room and made perfectly dry, and then the varnish may be applied with
a flat camel-hair brush made for the purpose. This must be done very
rapidly, but with great care; the same place should not be passed twice
over in laying on one coat if it can possibly be avoided. The best way
of proceeding is to begin in the middle and pass the brush to one end,
then with another stroke from the middle pass it to the other end, taking
care that before each stroke the brush be well supplied with varnish;
when one coat is dry another must be laid over it in like manner, and
this must be continued five or six times. If on trial there be not a
sufficient thickness of varnish to bear the polish without laying bare the
painting or ground colour underneath more varnish must be applied.
When a sufficient number of coats of varnish is so applied the work is
fit to be polished, which must be done in common work by rubbing it
with a piece of cloth or felt dipped in tripoli or finely ground
pumice-stone. But towards the end of the rubbing a little oil of any kind
must be used with the powder, and when the work appears sufficiently
bright and glossy it should be well rubbed with the oil alone to clean it
from the powder and to give it a still greater lustre. In the case of white
grounds, instead of the tripoli, fine putty or whiting should be used, but
they should be washed over to prevent the danger of damaging the
work from any sand or any other gritty matter that may happen to be
mixed with them. It greatly improves all kinds of japan work to harden
the varnish by means of heat, which, in every degree that can be
applied short of what would burn or calcine the matter, tends to give it
a firm and strong texture where metals form the body; therefore a very
hot stove may be used, and the stoving may be continued for a
considerable time, especially if the heat be gradually increased. But
where wood or papier-mâché is in question, heat must be applied with
great caution.
SECTION III.
JAPANNING OR ENAMELLING METALS.
In japanning metals, all good work of which should be stoved, they
have to be first thoroughly cleaned, and then the japan ground applied
with a badger or camel-hair brush or other means, very carefully and
evenly. Metals usually require from three to five coats, and between
each application must be dried in an oven heated from 250° to 300°
F.--about 270° being the average. It has already been seen that the best
grounds for japanning are formed of shellac varnish, the necessary
pigments for colouring being added thereto, being mixed with the
shellac varnish after they have been ground into a high degree of
smoothness and fineness in spirits of turpentine. In japanning it is best
to have the oven at rather a lower temperature, increasing the heat after
the work has been placed in the oven. When a sufficient number of
coats have been laid on--which will usually be two only--the work must
be polished by means of a piece of cloth or felt dipped in tripoli or
finely powdered pumice-stone. For white grounds fine putty
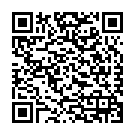
Continue reading on your phone by scaning this QR Code
Tip: The current page has been bookmarked automatically. If you wish to continue reading later, just open the
Dertz Homepage, and click on the 'continue reading' link at the bottom of the page.