find them of use.
[Illustration: FIG. 4.--ARRANGEMENT OF IMPROVED
DISCHARGER AND MAGNET.]
One of the changes is that the adjustable knobs A and B (Fig. 4), of the
discharger are held in jaws of brass, JJ, by spring pressure, this
allowing of turning them successively into different positions, and so
doing away with the tedious process of frequent polishing up.
The other change consists in the employment of a strong electromagnet
NS, which is placed with its axis at right angles to the line joining the
knobs A and B, and produces a strong magnetic field between them.
The pole pieces of the magnet are movable and properly formed so as
to protrude between the brass knobs, in order to make the field as
intense as possible; but to prevent the discharge from jumping to the
magnet the pole pieces are protected by a layer of mica, MM, of
sufficient thickness. s_1 s_1 and s_2 s_2 are screws for fastening the
wires. On each side one of the screws is for large and the other for
small wires. LL are screws for fixing in position the rods RR, which
support the knobs.
In another arrangement with the magnet I take the discharge between
the rounded pole pieces themselves, which in such case are insulated
and preferably provided with polished brass caps.
The employment of an intense magnetic field is of advantage
principally when the induction coil or transformer which charges the
condenser is operated by currents of very low frequency. In such a case
the number of the fundamental discharges between the knobs may be so
small as to render the currents produced in the secondary unsuitable for
many experiments. The intense magnetic field then serves to blow out
the arc between the knobs as soon as it is formed, and the fundamental
discharges occur in quicker succession.
Instead of the magnet, a draught or blast of air may be employed with
some advantage. In this case the arc is preferably established between
the knobs AB, in Fig. 2 (the knobs ab being generally joined, or
entirely done away with), as in this disposition the arc is long and
unsteady, and is easily affected by the draught.
When a magnet is employed to break the arc, it is better to choose the
connection indicated diagrammatically in Fig. 5, as in this case the
currents forming the arc are much more powerful, and the magnetic
field exercises a greater influence. The use of the magnet permits,
however, of the arc being replaced by a vacuum tube, but I have
encountered great difficulties in working with an exhausted tube.
[Illustration: FIG. 5.--ARRANGEMENT WITH LOW-FREQUENCY
ALTERNATOR AND IMPROVED DISCHARGER.]
[Illustration: FIG. 6.--DISCHARGER WITH MULTIPLE GAPS.]
The other form of discharger used in these and similar experiments is
indicated in Figs. 6 and 7. It consists of a number of brass pieces cc
(Fig. 6), each of which comprises a spherical middle portion m with an
extension e below--which is merely used to fasten the piece in a lathe
when polishing up the discharging surface--and a column above, which
consists of a knurled flange f surmounted by a threaded stem l carrying
a nut n, by means of which a wire is fastened to the column. The flange
f conveniently serves for holding the brass piece when fastening the
wire, and also for turning it in any position when it becomes necessary
to present a fresh discharging surface. Two stout strips of hard rubber
RR, with planed grooves gg (Fig. 7) to fit the middle portion of the
pieces cc, serve to clamp the latter and hold them firmly in position by
means of two bolts CC (of which only one is shown) passing through
the ends of the strips.
[Illustration: FIG. 7.--DISCHARGER WITH MULTIPLE GAPS.]
In the use of this kind of discharger I have found three principal
advantages over the ordinary form. First, the dielectric strength of a
given total width of air space is greater when a great many small air
gaps are used instead of one, which permits of working with a smaller
length of air gap, and that means smaller loss and less deterioration of
the metal; secondly by reason of splitting the arc up into smaller arcs,
the polished surfaces are made to last much longer; and, thirdly, the
apparatus affords some gauge in the experiments. I usually set the
pieces by putting between them sheets of uniform thickness at a certain
very small distance which is known from the experiments of Sir
William Thomson to require a certain electromotive force to be bridged
by the spark.
It should, of course, be remembered that the sparking distance is much
diminished as the frequency is increased. By taking any number of
spaces the experimenter has a rough idea of the electromotive
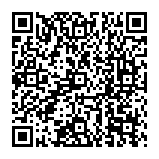
Continue reading on your phone by scaning this QR Code
Tip: The current page has been bookmarked automatically. If you wish to continue reading later, just open the
Dertz Homepage, and click on the 'continue reading' link at the bottom of the page.