a ton.
Suppose that the cost of the coal used in the foregoing test was $3.60
per ton of 2,000 pounds. The equivalent evaporation per pound of coal
was 7.5 pounds. Therefore the cost of evaporating 1,000 pounds of
water from 180° F. to steam at 100-pound gage, is--
$3.60 × 1,000 ------------- = $0.24, or 24 cents. 7.5 × 2,000
TABLE OF TEST RESULTS.
After the test has been made and properly worked up, as heretofore
described, collect all the results of the test on one sheet, so that they can
be kept in convenient form for reference and for comparison with later
tests. A brief form of arranging the results is as follows:
1. Date of test May 20, 1918 2. Duration of test hours 10 3. Weight of
coal used pounds 5,000 4. Weight of water fed and evaporated do.
35,000 5. Average steam pressure, gauge do. 100 6. Average
feed-water temperature °F. 180 7. Factor of evaporation 1.0727 8.
Equivalent evaporation from and at 212° F. pounds 37,545
EFFICIENCY.
9. Efficiency of boiler and furnace per cent 54
CAPACITY.
10. Boiler horsepower developed 109 11. Builders' rated horsepower
150 12. Percentage of rated horsepower developed per cent 73
ECONOMIC RESULTS.
13. Actual evaporation per pound of coal pounds 7 14. Equivalent
evaporation from and at 212° F. per pound of coal as fired, pounds 7.5
15. Cost of coal per ton (2,000 pounds) $3.60 16. Cost of coal to
evaporate 1,000 pounds from and at 212° F. $0.24
HOW TO USE THE TEST RESULTS.
The object of working up a test is to obtain a clear idea as to the
efficiency of operation of the boiler or its operating cost. Consequently,
after the calculations have been made, they should be used as a basis
for study with the idea of improving the boiler performance.
Take the matter of boiler efficiency, for example, as found from the test
mentioned. Its value was 54 per cent. This is altogether too low and
indicates wasteful operation. The efficiency of a hand-fired boiler
ought not to be less than 65 per cent, and it can be increased to 70 per
cent by careful management under good conditions.
The chart in figure 3 can be used to indicate the evaporation that should
be obtained in order to reach a desired efficiency. Suppose, for example,
that it is desired to know how much water per pound of coal must be
evaporated to produce a boiler efficiency of 65 per cent with coal
having a heating value of 13,500 B. t. u. per pound.
Locate 13,500 at the bottom of the chart, follow the vertical line until it
meets the diagonal marked 65 per cent, and then from this point follow
the horizontal line to the left-hand edge, where the figure 9 is found.
This means that the equivalent evaporation from and by 212° F. per
pound of coal must be 9 pounds of water. If the steam pressure is 100
pounds gauge, and the feed-water temperature is 180° F. the factor of
evaporation is 1.0727, then the actual evaporation must be 9 ÷ 1.0727 =
8.36 pounds per pound of coal. In other words, to increase the
efficiency from 54 per cent to 65 per cent under the same conditions of
pressure and feed-water temperature, it would be necessary to increase
the actual evaporation from 7 pounds to 8.36 pounds. This would mean
practically 20 per cent more steam from the same weight of coal used.
[Illustration: Heating Value of Coal, in B. t. u. Per Pound
FIG. 3.]
How to do this will require some study and experimenting on the part
of the fireman or engineer. The three most common reasons for
low-boiler efficiency are (1) excess air, (2) dirty heating surfaces, and
(3) loss of coal through the grates. The first of these items is the most
important of the three. In most cases the greatest preventable waste of
coal in a boiler plant is directly due to excess air. Excess air simply
means the amount of air which gets into the furnace and boiler which is
not needed for completing the combustion of the coal. Very often twice
as much air is admitted to the boiler setting as is required. This extra or
excess air is heated and carries heat out through the chimney instead of
heating the water in the boiler to make steam. There are two ways in
which this excess air gets into the furnace and boiler setting. First, by a
combination of bad regulation of drafts and firing. The chances are
your uptake damper is too wide open. Try closing it a little. Then, there
may be holes in the fire. Keep these covered. The second way excess
air occurs is by leakage through the boiler setting,
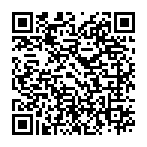
Continue reading on your phone by scaning this QR Code
Tip: The current page has been bookmarked automatically. If you wish to continue reading later, just open the
Dertz Homepage, and click on the 'continue reading' link at the bottom of the page.