happened to be in the
village getting orders for tools. As soon as his eye fell upon those
hammers, he saw their merits, and bought them all. He did more. He
left a standing order for as many hammers of that kind as David
Maydole could make.
That was the beginning. The young blacksmith hired a man or two,
then more men, and made more hammers, and kept on making
hammers during the whole of his active life, employing at last a
hundred and fifteen men.
During the first twenty years, he was frequently experimenting with a
view to improve the hammer. He discovered just the best combination
of ores to make his hammers hard enough, without being too hard.
He gradually found out precisely the best form of every part. There is
not a turn or curve about either the handle or the head which has not
been patiently considered, and reconsidered, and considered again, until
no further improvement seemed possible. Every handle is seasoned
three years, or until there is no shrink left in it.
Perhaps the most important discovery which he made was that a perfect
tool cannot be made by machinery.
Naturally, his first thought, when he found his business increasing, was
to apply machinery to the manufacture, and for some years several
parts of the process were thus performed. Gradually, his machines were
discarded, and for many years before his retirement, every portion of
the work was done by hand.
Each hammer is hammered out from a piece of iron, and is tempered
over a slow charcoal fire, under the inspection of an experienced man.
He looks as though he were cooking his hammers on a charcoal furnace,
and he watches them until the process is complete, as a cook watches
mutton chops.
I heard some curious things about the management of this business.
The founder never did anything to "push" it. He never advertised. He
never reduced the price of his hammers because other manufacturers
were doing so.
His only care, he said, had been to make a perfect hammer, to make just
as many of them as people wanted, and no more, and to sell them at a
fair price. If people did not want his hammers, he did not want to make
them. If they did not want to pay what they were worth, they were
welcome to buy cheaper ones of some one else.
For his own part, his wants were few, and he was ready at any time to
go back to his blacksmith's shop.
The old gentleman concluded his interesting narration by making me a
present of one of his hammers, which I now cherish among my
treasures.
If it had been a picture, I should have had it framed and hung up over
my desk, a perpetual admonition to me to do my work well; not too fast;
not too much of it; not with any showy false polish; not letting anything
go till I had done all I could to make it what it should be.
In telling this little story, I have told thousands of stories. Take the
word hammer out of it, and put glue in its place, and you have the
history of Peter Cooper. By putting in other words, you can make the
true history of every great business in the world which has lasted thirty
years.
The true "protective system," of which we hear so much, is to make the
best article; and he who does this need not buy a ticket for Colorado.
ICHABOD WASHBURN,
WIRE-MAKER.
Of all our manufactures few have had a more rapid development than
wire-making. During the last thirty years the world has been girdled by
telegraphic wires and cables, requiring an immense and continuous
supply of the article. In New York alone two hundred pianos a week
have been made, each containing miles of wire. There have been years
during which a garment composed chiefly of wire was worn by nearly
every woman in the land, even by the remotest and poorest.
Who has supplied all these millions of miles of wire? A large part of
the answer to this question is given when we pronounce the name at the
head of this article, Ichabod Washburn. In the last years of his life he
had seven hundred men at Worcester making wire, the product of
whose labor was increased a hundred fold by machinery which he had
invented or adapted.
It is curious to note how he seemed to stumble into the business just in
the nick of time. I say, seemed; but, in truth, he had been prepared for
success in it by a long course of experience and training. He was a poor
widow's son, born on the coast of Massachusetts, a few miles from
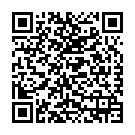
Continue reading on your phone by scaning this QR Code
Tip: The current page has been bookmarked automatically. If you wish to continue reading later, just open the
Dertz Homepage, and click on the 'continue reading' link at the bottom of the page.