file made of agate,
say one inch long, one-quarter inch wide and one-eighth inch thick. A
slip of this kind can be obtained from any lapidary, and after grinding
with emery and water until the surface has a very fine grain, it should
be mounted by fastening with cement into a brass socket and this is
then inserted into a small wooden handle, as shown in Fig. 17. The
agate slip should be ground to about the shape of B, Fig. 16, so that one
side can be used for square corners and the other for conical pivots. The
final polish can soon be imparted by means of a small boxwood slip, or
flattened peg-wood, and diamantine and alcohol. Never try to bring out
the final polish until you are satisfied that all graver marks have been
ground out, otherwise you will simply have to go all over the work
again.
[Illustration: Fig. 17.]
When the staff is finished from the lower pivot to the seat of the
balance, the upper part should be roughed out nearly to size and then
cut off preparatory to finishing the top part.
Attention was previously called to the fact that the majority of
watchmakers prefer to finish all the lower portion of the staff first,
notwithstanding the fact that there are numerous advantages to be
gained by proceeding to first finish up the upper portion. We have now
reached the point where the wax chuck must be used, and perhaps these
advantages may be now more clearly defined. In order that the two
procedures may be more distinctly shown, illustrations of both methods
are here given. Fig. 18 shows the popular method, the lower portion of
the staff being all completed and fastened by means of wax, in the wax
chuck. Fig. 19 shows the opposite course of procedure. In both
illustrations the lines indicate the amount of wax applied to hold the
work. It will be noted that in Fig. 18 the hub of the staff is enclosed in
the wax very much as a cork is fitted into a bottle, while in Fig. 19 the
hub is reversed, just as a cork would appear were the larger portion
within the bottle and the smaller portion protruding through the neck. A
study of the diagram will readily show that in Fig. 19 the staff is held
more rigidly in place and that a greater bulk of the work is enclosed in
the wax than in Fig. 18, although there is less wax used in the former
than in the latter.
[Illustration: Fig. 18.]
[Illustration: Fig. 19.]
Before proceeding to set the staff in the wax, it is necessary to make
some measurements to determine its full length. Remove both cap
jewels and screw the balance cock in place. Examine the cock and see
if it has at any time been bent up or down or punched to raise or lower
it. If so, rectify the error by straightening it and then put it in place.
Now with a degree gauge, or calipers, proceed to take the distance
between the outer surfaces of the hole jewels and shorten the staff to
the required length. Do not remove too much, but leave the staff a little
long rather than cut it too short, as the length can be shortened later.
[Illustration: Fig. 20.]
[Illustration: Fig. 21.]
A very handy tool for the purpose of making these length
measurements can be constructed by adding a stop screw to the
common double calipers as shown in Fig. 20. The improvement
consists in the fact that they can be opened to remove from the work
and closed again at exactly the same place, so that an accurate
measurement can be made. The all-important point in the use of wax
chucks is to get a perfect center. If you are not careful you are liable to
leave a small projection in the center as shown at A, Fig. 21. The
ordinary wax chuck cannot be unscrewed from the spindle and restored
to its proper place again with anything like a certainty of its being
exactly true, and if you insist on doing this there is no remedy left but
finding a new center each time. It will be found more satisfactory and
economical in the long run to have a permanent chuck for a wax chuck
and you will then have no necessity for removing the brass chuck.
The center, or cone for the reception of the pivot, should be turned out
with the graver at an angle of about 60° and such a graver as is shown
at B, Fig. 1, will answer admirably for this purpose. After you have
carefully centered your wax chuck, place a small alcohol lamp under
the chuck and heat it until the wax
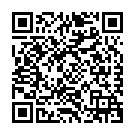
Continue reading on your phone by scaning this QR Code
Tip: The current page has been bookmarked automatically. If you wish to continue reading later, just open the
Dertz Homepage, and click on the 'continue reading' link at the bottom of the page.