cut the seat for the roller,
remove it from the foot of the gauge and apply the gauge to the work as
shown in Fig. 9. The foot of the gauge resting against the end of the
pivot, the taper end of the gauge will locate accurately the position of
the roller seat. In order to locate the proper position for the seat for the
balance, proceed the same as for the roller, except that the foot of the
gauge is lowered until it is brought sufficiently below the plate to allow
of the proper clearance as indicated by the dotted lines at H. Now apply
the gauge to the new staff, as shown in Fig. 10, and the taper end will
locate the exact position for the balance seat.
[Illustration: Fig. 9.]
[Illustration: Fig. 10.]
As previously stated, I have taken it for granted that you preferred to
finish all the lower portion of the staff while the work was held in the
chuck. I have assumed that you prefer to work in this way because I
have noted the fact that nine watchmakers out of every ten start with,
and first finish up, the lower portion of the staff. Where this method of
working originated I do not know, but it always has the appearance to
me of "placing the cart before the horse." I do not pretend to say that a
true staff cannot be made in this way, but it certainly is not the most
convenient nor advisable. We all know that the heaviest part of the staff
is from the roller seat to the end of the top pivot. Now it seems to me
that it is the most natural thing in the world for a mechanic to desire to
turn the greater bulk of his work before reversing it. Now if the
workman has been educated to turn indifferently with right or left hand,
it may make little difference, as far as the actual turning is concerned,
whether he starts to work at the upper or lower end of the staff, but
unfortunately there are few among us who are so skilled as to use the
graver with equal facility with either hand, and it is therefore an
advantage to start with the upper end, as you can thus finish a greater
portion of the work more readily. You can readily see that when you
come to reverse your staff and use the wax chuck, that by starting at the
top of staff your wax has a much larger surface of metal to cling to, and
again the shape of the balance seat is such as to secure the work firmly
in the wax, while if the reverse method is employed, the larger portion
of the balance seat is exposed and the staff is more liable to loosen
from the motion of the lathe and pressure of the graver and polishers.
CHAPTER IV.
By the aid of the pinion calipers and the old staff, the diameter of the
roller seat and the balance and hair-spring collet seats may be readily
taken, but it is perhaps better to gauge the holes, as the old staff may
not have been perfect in this respect. A round broach will answer
admirably for this purpose, and the size may be taken from the broach
by means of the calipers. In fitting our pivots, we can not be too exact;
and as yet no instrument has been placed upon the market for this
purpose which is moderate in price and yet thoroughly reliable. The
majority of watchmakers use what is termed the pivot-gauge, a neat
little instrument which accompanies the Jacot lathe, and which may be
obtained from any material house. This tool, which is shown in Fig. 11,
is, however, open to one objection in the measurement of pivots, and
that is that it may be pressed down at one time with greater force than
at another, and consequently will show a variation in two
measurements of the same pivot. Some of my readers may think that I
am over-particular on this point, and that the difference in measurement
on two occasions is too trivial to be worthy of attention, but I do not
think that too much care can be bestowed upon this part of the work,
and neglect in this particular is, I think, the cause of poor performance
in many otherwise good timepieces. The ordinarily accepted rule
among watchmakers is that a pivot should be made 1/2500 of an inch
smaller than the hole in the jewel to allow for the proper lubrication. I
am acquainted with watchmakers, and men who are termed good
workmen, too, who invariably allow 1/2500 of an inch side shake, no
matter whether the pivot is 12/2500 or 16/2500 of an
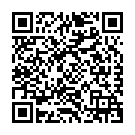
Continue reading on your phone by scaning this QR Code
Tip: The current page has been bookmarked automatically. If you wish to continue reading later, just open the
Dertz Homepage, and click on the 'continue reading' link at the bottom of the page.