market. This state of affairs leads to
makeshifts, and they in turn lead to botch work. The watchmaker who
does not possess the experience or necessary qualifications to make a
new balance staff and make it in a neat and workmanlike manner, is
never certain of having exactly what is needed, and cannot hope to long
retain the confidence of his customers. In fact, he is not a watchmaker
at all, but simply an apprentice or student, even though he be working
for a salary or be his own master. There are undoubtedly many worthy
members of the trade, who are not familiar with the making of a
balance staff, who will take exceptions to this statement; but it is
nevertheless true. They may be good workmen as far as they go; they
may be painstaking; but they cannot be classed as watchmakers.
This article is intended for the benefit of that large class whose
opportunities for obtaining instruction are limited, and who are ready
and willing to learn, and for that still larger class of practical workmen
who can make a new staff in a creditable manner, but who are always
glad to read others people's ideas on any subject connected with the
trade and who are not yet too old to learn new tricks should they find
any such.
[Illustration: Fig. 1.]
Good tools, in good condition, are the most essential requisites in
making a new staff. I would not advise any particular make of lathe, as
the most expensive lathe in the world will not produce a true staff if the
workman cannot center his work accurately and does not know how to
handle his graver, while on the other hand fine work can be done on the
simplest and cheapest lathe by a workman possessing the requisite skill.
I will take it for granted that you use an American-made lathe of some
kind, or a foreign-made lathe manufactured on American lines. It is
advisable, though not absolutely necessary, to have three gravers
similar to those illustrated in Fig. 1, A being used for turning the staff
down in the rough; B for the conical pivots and square shoulders and C
for the under-cutting. The other tools and attachments needed will be
described as I come to them in use.
The balance staff should be made of the best steel, tempered to such a
degree as to give the longest service and yet not so hard as to endanger
the breakage of the pivots. Select a piece of Stubb's steel wire, say No.
46, or a little larger than the largest part of the finished staff is to be,
and center it in a split chuck of your lathe. Be careful in selecting your
chuck that you pick one that fits the wire fairly close. The chuck holds
the work truest that comes the nearest to fitting it. If you try to use a
chuck that is too large or too small for the work, you will only ruin the
chuck for truth. Turn the wire to the form of a rough staff, as shown in
Fig. 2, leaving on a small part of the original wire, as shown at A. After
the wire is roughed out to this general form, remove from the chuck
and get ready to harden and temper it. The hardening and tempering
may be effected in various ways, and I am scarcely prepared to say
which method is the best, as there are several which give about the
same general results. One method of hardening is to smear the blank
with common yellow soap, heat it to a cherry red, and drop endwise
into linseed oil. Petroleum is preferred by some to linseed oil, but, to
tell the truth, I can see no difference in the action of linseed, petroleum
or olive oil. Be sure and have enough oil to thoroughly cool the blank,
and a deep vessel, such as a large-mouthed vial, is preferable to a
saucer. The blank will now be found too hard to work easily with the
graver, and we must therefore draw the temper down to that of fine
spring steel. Before doing this the blank should be brightened, in order
that we may see to just what color we are drawing it. The main object
in using the soap in hardening is that it may form a scale upon the
blank, and if the heating is effected gradually the soap will melt and
form a practically air-tight case around the blank. This scale, if the
hardening is carefully and properly done, will generally chip and fall
off when the blank is plunged in the oil, particularly if the oil is cool,
and if it does not fall off of its own accord, it can easily be removed by
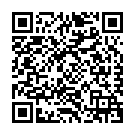
Continue reading on your phone by scaning this QR Code
Tip: The current page has been bookmarked automatically. If you wish to continue reading later, just open the
Dertz Homepage, and click on the 'continue reading' link at the bottom of the page.